August 06, 2024 – Engineering Plastics: Redefining Material Performance and Industry Boundaries
In the realm of high-performance polymers, engineering plastics have emerged as a formidable force, capable of enduring mechanical stress across a broad temperature spectrum and thriving in harsh chemical and physical environments. Since their inception in the 1950s, these advanced materials have permeated diverse sectors, including electronics, automotive, and construction, progressively supplanting metallic counterparts in a global trend known as ‘plastics for steel’ and ‘plastics for wood.’
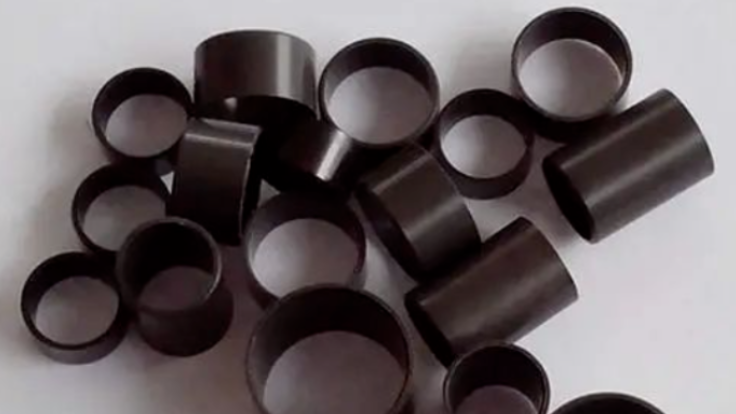
At the crux of selecting engineering plastics lies the material’s thermal endurance. Strategically incorporating reinforcements such as glass or carbon fibers not only bolsters heat resistance and raises the temperature threshold for deformation but also cuts costs, enabling plastic to rival metal in select applications. Carbon fiber infusion, in particular, confers exceptional stiffness, reduced density, and enhanced electrical conductivity and tribological properties, hence its prevalence in automotive fuel lines and beyond.
Hardness, another cornerstone property, though naturally inferior to metals, is addressable through innovative designs, structural reinforcements, and the utilization of low-density formulations. Moreover, the integration of fillers and fibers significantly augments plastic rigidity, narrowing the gap with metallic materials.
When it comes to impact resistance, polycarbonates and their blends excel at ambient temperatures, suitable for continuous operation up to 100-120°C. Liquid crystal polymers, meanwhile, showcase remarkable toughness, further expanding the horizons of engineering plastics.
Their self-lubricating and wear-resistant characteristics are equally noteworthy, particularly advantageous in friction-intensive applications like gears and pump rotors. By incorporating additives like graphite or polytetrafluoroethylene, friction coefficients plummet, and wear resistance soars.
Chemical resistance is another stronghold, with semi-crystalline polymers like fluoropolymers and polyphenylene sulfides maintaining robust chemical stability even at elevated temperatures, making them ideal for demanding environments like engine compartments and pump systems. Additionally, engineering plastics’ resilience to UV radiation and gamma rays underscores their versatility in specialized applications.
As reported by AsiaMB, the relentless advancement of material science propels engineering plastics into ever-wider industrial adoption, heralding a new era where traditional materials are increasingly supplanted by these innovative polymers.