April 28, 2025 – The discoloration of flame-retardant modified materials during processing and storage has long been a persistent headache for chemical manufacturing enterprises. This issue not only undermines the visual quality of products but also risks eroding customer trust and dampening market sales. So, what exactly are the culprits behind the discoloration of flame-retardant modified materials? After in-depth industry research and analysis, the main causes can be summarized into five key aspects.
Firstly, the stability variance of raw materials emerges as a crucial factor. Some resins on the market, due to the lack of added antioxidants or stabilizers during production, cause plastic products to discolor right after extrusion. In some cases, the discoloration also occurs during storage. However, when switching to resins from other manufacturers or brands, the problem disappears immediately. This phenomenon vividly exposes the inconsistent quality of resin products. Evidently, selecting and using raw materials with excellent stability is the primary step in ensuring product quality.
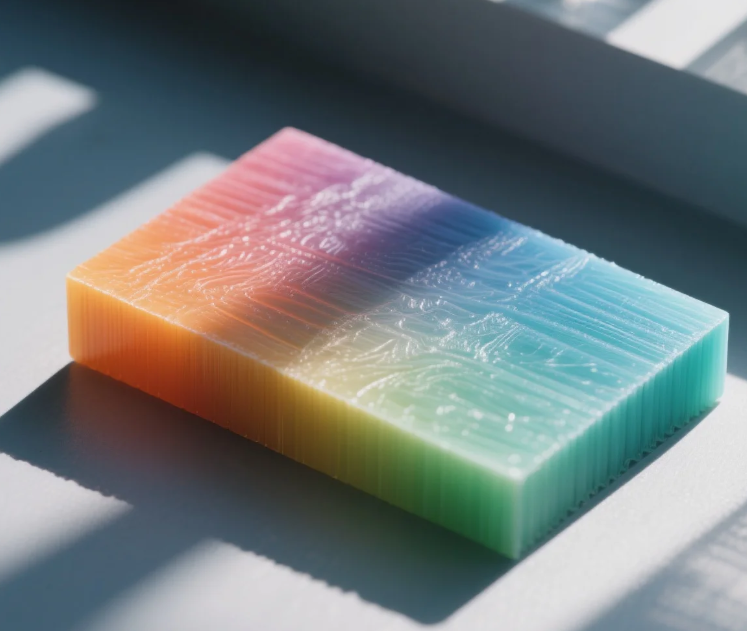
Secondly, the high-temperature resistance of flame retardants plays a vital role. When flame retardants decompose at temperatures lower than the normal processing temperature of materials, they generate small-molecule substances, which in turn cause the color of the entire system to change. Take common plastics as examples: the processing temperature of PP ranges from 170 – 230°C, PA6 from 230 – 290°C, and PA66 from 240 – 310°C. Different plastics require different types of suitable flame retardants. If the wrong flame retardant is chosen and it cannot withstand the processing temperature, discoloration becomes inevitable.
According to insights from AsiaMB, excessive metal impurities in fillers are also “invisible threats.” Impurities such as iron, nickel, and chromium undergo incomplete oxidation under certain conditions, forming oxides that lead to the discoloration of plastic products. For instance, the oxidation of iron in the air produces red iron oxide, making the product color darken. Commonly used fillers like titanium dioxide and calcium carbonate may pose a discoloration risk once their impurity content exceeds the standard.
Moreover, the interactions among various processing and modification additives cannot be overlooked. Additives such as antioxidants and plasticizers must neither react with each other during high-temperature processing nor decompose due to oxidation. If the compatibility or stability of these additives is insufficient, it will also result in product discoloration.
Finally, the impact of environmental factors should not be underestimated. Substances like NOx in the air are inherently colored. For example, reddish-brown nitrogen dioxide, when adhering in large quantities to the exposed edges of plastic products, causes edge discoloration. Additionally, external conditions such as light and heat can also trigger chemical reactions in plastic components, leading to degradation and discoloration.
The discoloration of flame-retardant modified materials has complex causes, spanning multiple dimensions including raw materials, additives, and the environment. For engineers, only by comprehensively considering all influencing factors and implementing multi-faceted measures, from raw material control and process optimization to environmental management, can the color quality of products meet market and customer requirements, thus achieving a win-win situation for both enterprises and customers.