December 6, 2024 – Unraveling the Essentials of Black Color Masterbatch for Plastic Production
In the realm of plastic molding and processing, black color masterbatch stands as a pivotal additive known to all. Its versatility spans across, anti-aging, and electrically conductive products. However, manufacturers frequently encounter challenges when using it. Today, AsiaMB delves into the crucial aspects of black color masterbatch, aiming to provide valuable insights.
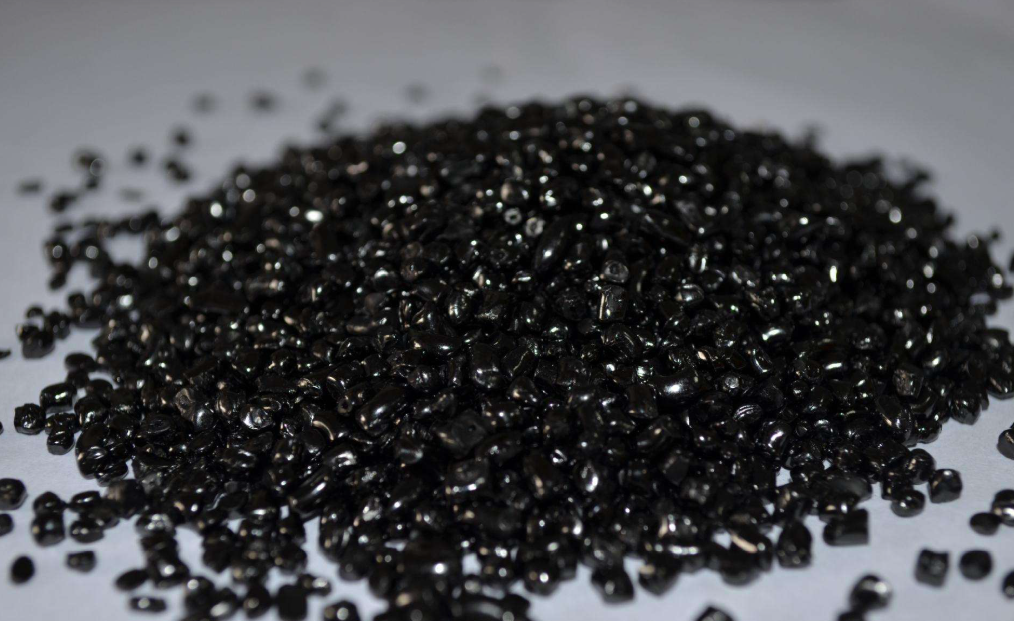
Firstly, let’s dissect the composition of black color masterbatch. It’s not a monolithic material but a meticulous blend of various components. Carbon black serves as the primary coloring agent, while a carrier holds the carbon black, a wetting agent aids in its dispersion, and a dispersant enhances uniformity within the carrier. Additional processing aids optimize the manufacturing process.
Discussing carbon black necessitates mentioning its diversity. According to international classifications, China boasts over 30 types, broadly categorized into rubber and non-rubber grades. Within the rubber industry, abrasion-resistant carbon black is crucial for tire durability. In non-rubber applications, fewer types are suitable for color masterbatches. Among them, channel black dominates plastic applications due to its wide availability, high purity, and small particle size. Channel black further categorizes into high, medium, and low pigment varieties, each with distinct pricing and performance.
What role does the carrier play? Simply put, it’s the “vehicle” for carbon black, influencing its dispersion and compatibility in plastics. The carrier material mirrors the plastic being colored; for instance, PS-based plastics use PS carriers in their black masterbatch, while LDPE is preferred for polyethylene due to its excellent carbon black loading and processing capabilities. For PP plastics, only PP or LDPE-based masterbatches are suitable.
Lastly, the significance of carbon black wetting agents cannot be overlooked. Carbon black, light and fluffy due to its small particle size and low density, requires wetting for smooth processing. The choice of wetting agent is crucial, impacting the processability of the masterbatch and the final product’s strength. Some companies opt for cost-cutting measures like excessive white oil or paraffin, compromising product strength. Balancing cost and performance is vital when selecting wetting agents to ensure product quality.
AsiaMB understands that as the plastics industry evolves, so do the demands for black color masterbatch. Future production will emphasize technological innovation and product quality to meet market demands.