May 23, 2025 – In the dynamic landscape of material coloration, color oil—a colloidal or suspension system formed by uniformly integrating pigments or dyes into an oily medium—has emerged as a cornerstone. Renowned for its exceptional fluidity, covering power, and adhesion properties, this versatile solution has become indispensable across diverse industries, from coatings and inks to plastics, rubber, and even cosmetics, enabling vibrant and durable coloring for a wide range of materials.
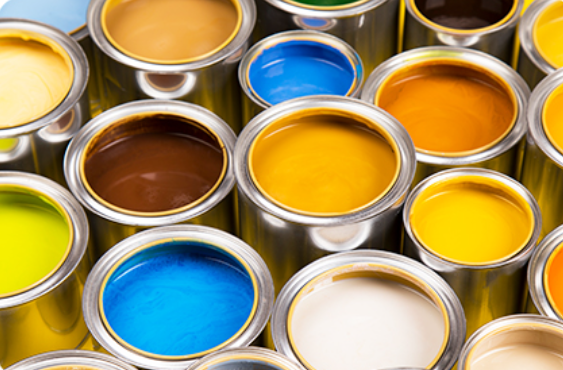
The performance of color oil is a culmination of its meticulously balanced components. At its core lie pigments or dyes, the primary sources of its chromatic appeal. Pigments, existing as micron-sized solid particles, are insoluble in the medium, imparting excellent hiding power and weather resistance. Their selection hinges on critical factors such as particle size, shape, and chemical stability. In contrast, dyes—soluble substances that offer vivid hues but slightly lower lightfastness—are ideal for applications requiring transparent or translucent effects. Notably, in specialized fields like food and pharmaceuticals, color oil formulations must adhere to strict non-toxic or low-toxicity standards.
The oily medium serves as both the carrier and a defining factor in color oil’s characteristics. Natural oils such as linseed oil and tung oil, with their moderate drying rates, remain staples in traditional coatings. Synthetic resins like acrylic and polyurethane, meanwhile, allow precise adjustment of viscosity and flexibility, meeting the demands of industrial production. Parameters such as drying speed, viscosity, and chemical stability directly influence the film-forming quality and production efficiency of color oil.
Dispersants play a pivotal role in maintaining the stability of color oil by preventing pigment sedimentation and agglomeration. Through the action of surfactants or polymers, they ensure uniform distribution of pigments within the oily medium. The selection of dispersants requires careful consideration of their dispersion efficiency, long-term stability, and compatibility with the oily matrix.
Functional additives, or auxiliaries, further refine color oil’s performance. Driers accelerate the curing process, leveling agents enhance coating smoothness, and defoamers minimize production defects. The type and dosage of these auxiliaries are dynamically optimized according to specific application scenarios to achieve optimal results.
According to industry insights from Color Masterbatch Industry Network, color oil finds particularly extensive use in the coatings sector, spanning interior and exterior wall decoration and protection for architectural coatings, anti-corrosion and aesthetic solutions for automotive and marine industrial coatings, and specialized fire-resistant and high-temperature-resistant formulations. In printing and packaging, color oil is deployed as ink in book publishing, inkjet printing, and screen printing, ensuring high-precision color reproduction. It also delivers long-lasting color and weather resistance to plastic and rubber products, including injection-molded parts, films, and tires. Emerging applications are also gaining traction, such as oil-soluble pigments in cosmetics like lipsticks and eyeshadows, and non-toxic coloring solutions for food and pharmaceutical industries.
Looking ahead, the evolution of color oil is poised to be driven by several key trends. In environmental sustainability, the focus will shift toward water-based color oils, bio-based raw materials, and low-toxicity formulations to reduce VOC emissions. For performance enhancement, 研发 efforts will concentrate on improving weather resistance, chemical resistance, and developing functional variants with fireproof and antibacterial properties. The integration of intelligence may enable color oils with adjustable hues, self-healing capabilities, or responsive features to environmental stimuli like temperature and light. Nanotechnology is set to revolutionize the field through the use of nano-pigments and dispersants, enhancing performance, while nanocomposites could introduce entirely new functionalities. Digitally, advancements in color management systems, 3D printing color oils, and virtual color-testing technologies are expected to drive innovation and efficiency across the industry.