April 27, 2025 – In plastic product manufacturing workshops, the seemingly minor issue of color deviation actually conceals a significant cost pitfall. Industry data reveals that color discrepancies in plastic products lead to a staggering 5% scrap rate, largely due to companies’ insufficient understanding of pigments and color masterbatches. Behind this multi – billion – dollar coloring market, what is the underlying logic? Let’s delve into the details.
In the realm of plastic coloring, pigments, as the core elements, follow unique classification patterns. Classified by chemical properties, they are divided into two main categories: organic and inorganic pigments. Among organic pigments, the azo red – yellow series is commonly used to create vibrant colors; many of Pantone’s Color of the Year selections are formulated with these pigments. Phthalocyanine blue – green, with its excellent color performance, is a key component in Tesla’s car paint. For inorganic pigments, titanium dioxide, with its high hiding power, is the top choice for white home appliance casings, while carbon black, due to its outstanding durability, safeguards the color of car bumpers. In terms of functional characteristics, pearlescent pigments can endow products with a starry visual effect, and their prices are comparable to silver. Fluorescent systems act as a “night – vision system” for highway reflective signs, boosting luminous efficiency by 300%.
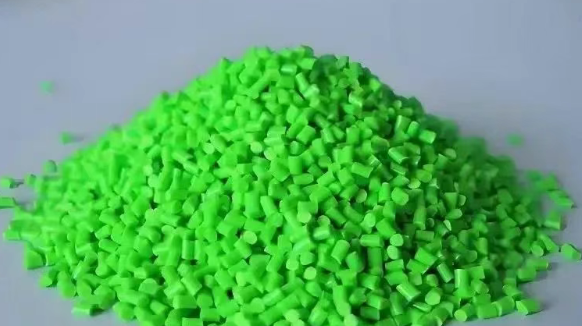
The advent of color masterbatches can be regarded as an industrial revolution in plastic coloring. In practical applications, they address production challenges from six dimensions. Precise matching of carrier resins is crucial. PP color masterbatches, with their high – temperature resistance of up to 120℃, serve as the “color identity” for takeout food containers. PET color masterbatches, certified as food – grade by the FDA, provide transparent protection for mineral water bottles. Function stacking endows color masterbatches with endless possibilities. Antibacterial color masterbatches form an “invisible shield” in the medical equipment field, with a bacteria – inhibiting rate of up to 99.99%. Conductive color masterbatches act as electromagnetic protection for 5G base station casings, controlling surface resistance to <10³Ω. According to AsiaMB, color masterbatch products in the current market are evolving towards greater specialization and functionality.
Facing complex production requirements, companies should make scientific decisions when selecting pigments and color masterbatches. For small – batch custom production (less than 1 ton), using direct pigments with twin – screw granulation is more cost – effective. The film blowing process demands high masterbatch fluidity, so special masterbatches with a melt index >20g/10min should be selected. For the production of automotive interior parts, weather – resistant color masterbatches certified by TS16949 are essential to ensure product quality.
The industry is evolving rapidly, and 2024 witnessed several disruptive trends in the plastic coloring field. Digital masterbatch technology has emerged. BASF’s intelligent color masterbatches can monitor stress distribution in products in real – time, providing accurate data support for the production process. Dow’s bio – based color masterbatches, with a 65% reduction in carbon footprint, have successfully entered Apple’s supply chain, driving the industry towards carbon neutrality. Domestic enterprises have achieved a major breakthrough in nano – dispersion technology, realizing a 3nm – level dispersion process and increasing color strength by 40%, breaking foreign technological monopolies.
However, in actual production, companies may face sharply increased costs if they fall into cognitive 误区. Blindly pursuing high – concentration color masterbatches (over 50%) can easily cause product brittleness. Using ordinary titanium dioxide in PC materials can lead to thermal degradation at high temperatures. Ignoring the compatibility parameters between color masterbatch carriers and substrates also affects product quality. These lessons highlight the importance of scientific selection and standardized use in the plastic coloring process.
As the application areas of plastic products continue to expand, the significance of the pigment and color masterbatch market becomes increasingly prominent. Only by deeply understanding the industry’s underlying logic and keeping up with technological trends can companies effectively reduce production costs, enhance product competitiveness, and secure a position in this multi – billion – dollar market.编辑分享