September 02, 2024 – The nylon industry in China has recently witnessed a rapid development phase. Major players such as Sanning Chemical, NHU, and Henan Xinlianxin Chemical have invested heavily in nylon new material projects, with a total investment exceeding billions of yuan. The commissioning of these projects is expected to significantly boost the domestic production capacity of nylon 66 and nylon 6, potentially reducing reliance on imported products.
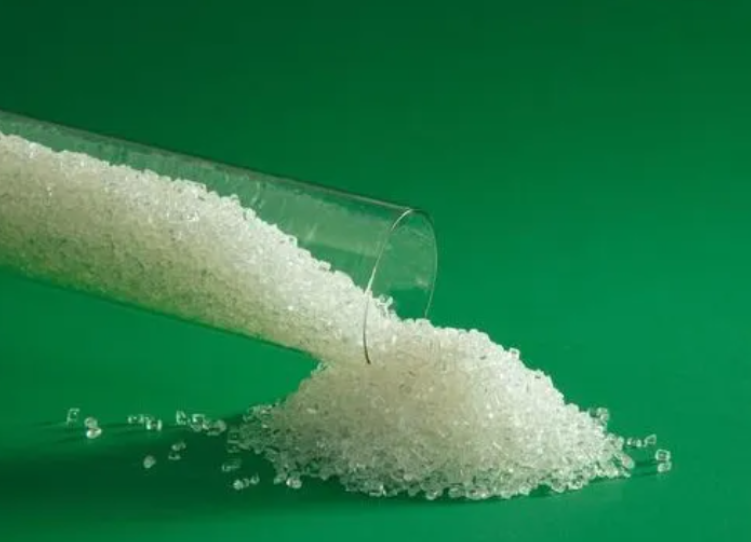
As the nylon industry thrives, the overall landscape of engineering plastics in China is undergoing transformations. Engineering plastics can be categorized into general-purpose and specialty engineering plastics. General-purpose engineering plastics, including polyamide (PA) and polycarbonate (PC), occupy a significant position in the domestic market. Meanwhile, specialty engineering plastics like polyphenylene sulfide (PPS) and polyimide (PI) are experiencing growing market demand due to their high performance and specialized applications, despite their relatively smaller consumption volume.
Within the domain of general-purpose engineering plastics, nylon 6 and nylon 66, both subtypes of polyamide (PA), are representative products, accounting for approximately 90% of total consumption. In recent years, China’s dependence on imported PA6 has gradually decreased, while the localization process of PA66 has accelerated, leading to a substantial increase in production capacity. According to institutional predictions, by 2032, China’s market share of PA6 and PA66 will reach 40%, becoming a major growth driver in the future.
On the other hand, the polycarbonate (PC) market faces an oversupply situation, resulting in declining prices and market size. However, in high-end electronic appliances and automotive parts industries, domestic products such as polyoxymethylene (POM) and polybutylene terephthalate (PBT) still rely on imports, making it difficult to significantly replace imported products in the short term.
In the field of specialty engineering plastics, although domestic products still need improvement in production processes and quality, the implementation of anti-dumping tariffs has created development opportunities for domestic PPS manufacturers. Additionally, domestic polyimide (PI) manufacturers have strong industrialization capabilities in the traditional electrical insulation field but have a lower market share in high-end areas. The demand for specialty engineering plastics such as polyetheretherketone (PEEK) and liquid crystal polymer (LCP) is also growing in the domestic market.
According to AsiaMB, despite facing challenges such as the need for industrial structure adjustment and technical support enhancement, the government and enterprises have made efforts in increasing research and development investments, promoting industry-university-research cooperation, and strengthening the standard system. Looking ahead, the domestic high-performance polymer material system will continue to improve, gradually achieving self-reliance and self-improvement development goals. It is estimated that by 2030, a relatively complete technical and industrial system will be established, realizing self-sufficiency in high-end grades. By 2050, it is expected to reach the world’s leading level.