December 4, 2024 – Teijin Carbon Fibers Announces Breakthroughs in Thermoplastic Composites Market
Teijin Carbon Fibers, a global leader in carbon fiber production and formerly known as Toho Tenax Co., Ltd. in Tokyo, Japan, has recently unveiled its latest advancements in the thermoplastic composites market. As a long-standing pioneer in the carbon fiber industry, Teijin’s Tenax thermoplastic tapes produced in Heinsberg, Germany, have gained worldwide recognition.
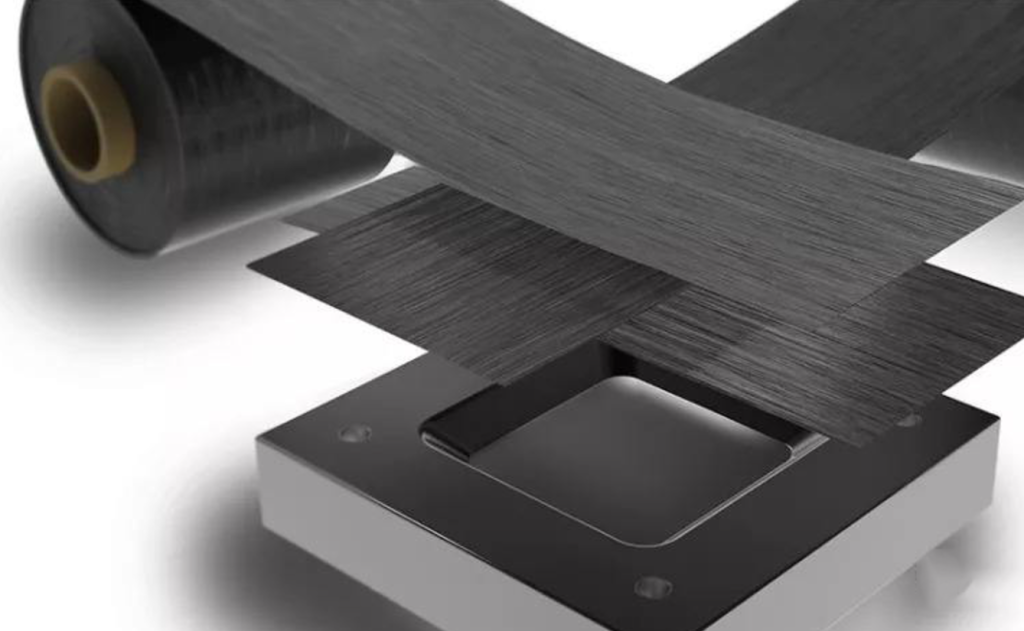
Looking back, Teijin has invested considerable time and effort into the research and development of thermoplastic materials. According to Jean-Philippe Canart, Aerospace Market Engineer at Teijin Carbon Fibers America and former Product Manager for Thermoplastic Semi-Finished Products at Toho Tenax Europe, the company’s journey in thermoplastic development began years ago. “Our successful launch of Unidirectional (UD) thermoplastic tapes in 2013 was a crucial part of our strategy,” Canart stated.
Discussing the foundation of this development, Canart emphasized, “One of our core technologies is the thermoplastic sizing for carbon fibers, which is vital for tape processing. Standard carbon fiber sizings must be removed due to the high temperatures involved in thermoplastic processing. Our thermoplastic sizing, however, is not only heat-resistant but also enhances the adhesion between fibers and the matrix in the finished composite, providing additional performance.” Industry sources reveal that Teijin’s largest production line in Europe can produce up to 1,700 tons of carbon fiber with TP sizing annually. Leveraging this advantage, Teijin has successfully developed UD tapes using PEEK, PEKK, and PPS thermoplastic matrix materials, primarily for aerospace applications, but also showing promising potential in the oil, gas, and industrial sectors.
The first significant application of Teijin’s thermoplastic composites was providing PEEK-coated carbon fiber fabric stamped clips and brackets for the Airbus A350. Canart noted, “This was the first major wave of aviation applications. Now, we’re seeing larger and more structural components shifting towards being made from AFP laminate hybrids and consolidated through stamping.” However, regarding In-Situ Consolidation (ISC) technology, Canart believes it still requires further maturation despite years of development. Teijin is actively supporting related research projects and institutes to drive this technology forward.
Looking ahead, Canart expressed that while the commercialization of ISC components may take time, with parts for commercial fuselages expected to be produced around 2025-2030, Teijin already sees a growing demand for thermoplastic composite tapes in two-step, AFP+stamping production lines. “We’ve invested in our European tape production lines and are supporting new process capabilities, such as Continuous Compression Molding (CCM),” Canart said. “With the supply chain continuously growing, we are confident in the future of thermoplastic composites.”