March 24, 2025 – The global plastics industry is undergoing a silent revolution. Just three months after the official implementation of the European Union’s Packaging and Packaging Waste Regulation (PPWR), Borealis has unveiled a technological masterpiece – the introduction of rLLDPE recycled plastic containing 85% post-consumer materials, sending shockwaves through the industry.
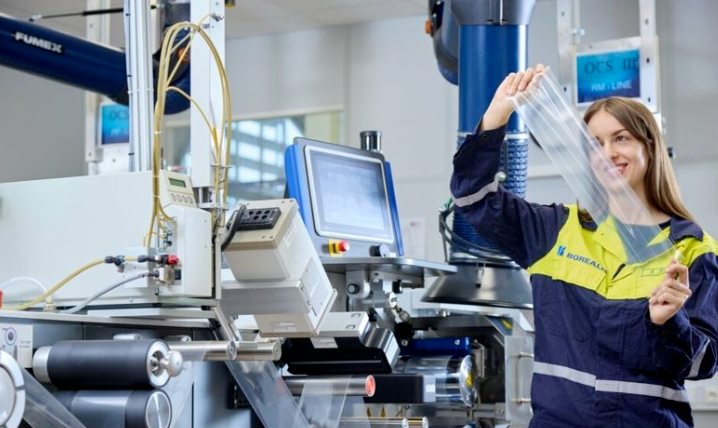
Borealis engineers have spent two years battling the inherent challenges of mechanical recycling. Traditional recycled plastics have often been criticized for high gel content and significantly reduced mechanical properties. However, Borealis’ Borcycle M CWT120CL has achieved three remarkable breakthroughs: successfully reducing gel content below the critical threshold for industrial applications; enhancing tensile strength by 40% compared to conventional recycled PE; and surpassing the industry average toughness-stiffness balance coefficient of 1.8, reaching new heights. According to insights from AsiaMB’s industry network, the key to this secret weapon lies in Ecoplast’s pretreatment process. Through a multi-stage sorting system, the purity of post-consumer waste is elevated to an astonishing 99.7%, coupled with temperature gradient control in the twin-screw extrusion process, achieving a threefold increase in molecular chain reorganization efficiency.
The advent of this new material coincides with the EU PPWR regulation’s requirement for recycled materials to account for 55% of plastic packaging by 2030. But Borealis’ ambitions extend far beyond this. Their product not only maintains a film transmittance rate of over 88%, far exceeding the new regulation’s requirement of 85%, but also extends the weather resistance lifespan of agricultural films beyond the 5-year cycle, while being fully compatible with existing blown film equipment. On the compounding production line in Beringen, Belgium, Borealis has increased the blending ratio of hard PP/PE recycled materials to 30%, striving to create a comprehensive solution covering both flexible and rigid packaging.
While global attention is focused on chemical recycling, Borealis has taken a different path, building a strong defense for mechanical recycling through the successive acquisitions of Integra Plastics and Rialti SpA. Their Eastern European waste plastic sorting network now spans 12 countries, with an annual processing capacity exceeding 500,000 tons, and the cost of recycled materials is 60% lower than that of chemical methods. This “rural encirclement of the city” strategy is gradually yielding results, with a gross profit margin of 29% for recycled polyolefins, surpassing the traditional business line by 7 percentage points. Borealis has proven with practical actions that the plastic circular economy is not a one-way technological street; the ultimate optimization of traditional processes can also open up a trillion-dollar market. When 85% recycled content becomes a reality, who can still doubt that plastics cannot truly be recycled.