May 13, 2025 – In the production and application of color masterbatches, black color masterbatches hold a significant position due to their extensive uses. However, producing high – quality black color masterbatches is no easy feat. Their quality needs to be controlled from several key aspects, with color dispersion, covering power, fluidity, and compatibility being the core elements for evaluating the quality of black color masterbatches.
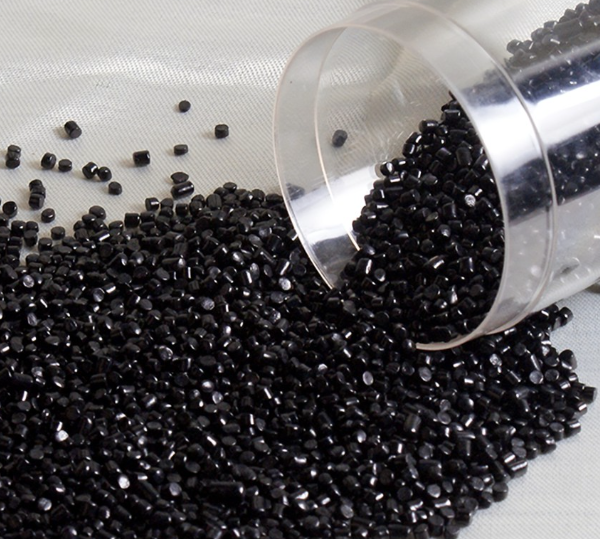
Black color masterbatches mainly use carbon black as the raw material. However, raw carbon black is prone to causing pollution and is difficult to disperse. Directly using raw carbon black for injection molding results in poor coloring effects, often accompanied by streaks and spots. Even when color masterbatch manufacturers produce high – load black color masterbatches using single or twin – screw extruders, the color dispersion is often unsatisfactory. According to the Color Masterbatch Industry Network, to achieve highly stable color dispersion, mixers with strong shearing capabilities, such as FCM or BANBURY, are required. Additionally, the type of carbon black significantly impacts the dispersion effect; the smaller the particles, the greater the dispersion difficulty. In fields with extremely high requirements for color dispersion, such as film and fiber production, poor dispersion not only affects the appearance of products but also reduces film performance and may even cause fiber production to halt.
Covering power is also a crucial factor determining the quality of black color masterbatches, especially in applications involving waste materials or recycled polymers. Black color masterbatches need to have strong covering power to mask other colors in the waste materials. Carbon black with large particles has weak coloring ability and cannot fully cover the underlying colors, thus affecting the color of the final product. During the melting process, choosing carbon black with high coloring ability to achieve good covering effects demonstrates the covering power of black color masterbatches.
Moreover, rheology and fluidity cannot be overlooked. Even if a color masterbatch has good color dispersion, if it cannot smoothly blend into the material to be molded, the production results will still fall short of expectations. Generally, the base resins used for producing color masterbatches have high rheology. However, some manufacturers use recycled materials, waste materials, or recycled plastics as resin carriers to reduce costs, which significantly decreases the fluidity of color masterbatches and causes numerous problems during the molding process.
Finally, compatibility is also an important indicator for measuring the quality of black color masterbatches. Color masterbatches produced from scraps or recycled materials may contain contaminants or non – meltable polymers, leading to production failures. Selecting appropriate base resins for producing color masterbatches can ensure good compatibility during the melting process. Currently, major international color masterbatch manufacturers are committed to developing “globally universal” color masterbatches. These color masterbatches feature strong compatibility and excellent rheology, promising to bring more efficient and flexible application experiences to the industry.