May 26, 2025 – High-Temperature Resistant Materials: Pioneering Innovations Across Industries with Thermal Fortitude
In the realm of chemical engineering, high-temperature resistant materials have emerged as indispensable assets, with plastics, rubbers, and fibers redefining performance benchmarks in extreme thermal environments. These materials are transforming industries by combining durability, stability, and efficiency in ways previously unattainable.
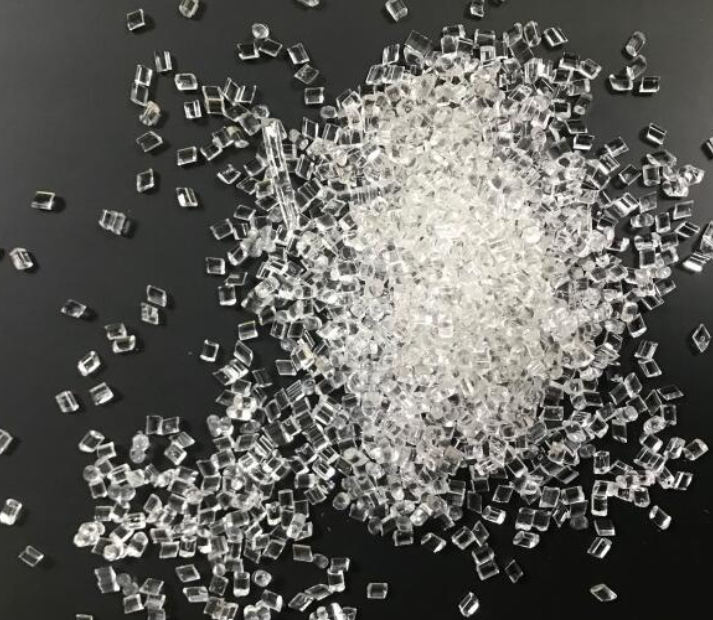
High-Temperature Plastics: Redefining Thermal Boundaries
High-temperature plastics excel in maintaining structural integrity and chemical resistance under scorching conditions. Polyimide stands out as a poster child, enduring temperatures ranging from -269°C to 400°C for prolonged use and surpassing 500°C briefly. NASA’s spacecraft rely on polyimide-based composites for thermal shielding, withstanding 1,650°C heat during atmospheric re-entry at 28,000 km/h, safeguarding critical components. In automotive engineering, polyphenylene sulfide (PPS) is a game-changer, enabling engine sensors to function flawlessly above 200°C with dimensional stability errors below 0.1%. PPS-based exhaust systems reduce vehicle weight by 5–10%, boosting fuel efficiency by 3–5% and curbing CO₂ emissions by 4%. The electronics sector leverages polyetheretherketone (PEEK), which retains electrical insulation (volume resistivity >10¹³ Ω·cm) at 150°C, as seen in Apple’s MacBook Pro heat modules. Liquid crystal polymers (LCPs) shine in 5G infrastructure, lowering signal loss by 30% in high-frequency transmission lines with a heat deflection temperature of 350°C. Innovators like BASF are pushing limits with novel polyamides targeting 260°C operational temperatures and 20–30% cost reductions, while Oak Ridge National Laboratory aims to recycle polyimide with 80%+ efficiency via chemical recycling.
High-Temperature Rubbers: Resilience in Extremes
Specialty high-temperature rubbers outperform conventional counterparts by sustaining elasticity and sealing performance above 150°C. Formulated with phenyl silicones, boron silicones, or phenylene silicones and reinforced with heat stabilizers, these rubbers resist deformation and maintain sealing integrity. A case in point: a chain-grade rubber operates continuously at 350°C for hours, peaking at 400°C. In automotive engines, where temperatures exceed 150°C, these rubbers extend seal lifespan from months to 3–5 years, slashing maintenance costs. Industrial pipelines handling 200–300°C media benefit from rubber gaskets that reduce heat loss by 20–30% while preventing leaks. Their resistance to chemicals, UV exposure, and mechanical stress makes them ideal for harsh environments, adapting seamlessly to diverse sealing geometries.
High-Temperature Fibers: Fortifying Structures Against Heat
High-temperature fibers like aramid and ceramic fibers outclass conventional fibers by retaining 80%+ tensile strength above 300°C. Aramid fibers, withstanding 260°C continuously and 500°C instantaneously, owe their strength to rigid molecular chains. Ceramic fibers excel at 1,200–1,600°C, offering superior thermal insulation. In protective gear, firefighter suits blended with aramid resist 800–1,000°C flames for 15+ seconds, reducing burn injuries by 60%. Construction uses ceramic fiber insulation to cut heat transfer by 40–50%, while aerospace employs carbon-fiber-reinforced ceramic composites in engine hot sections, boosting efficiency by 15–20% versus metals. Automotive applications include heat shields that lower engine bay temperatures by 30–50°C, enhancing component longevity. These fibers also resist acids, alkalis, and humidity, ensuring longevity in corrosive or high-moisture settings.
As industries push thermal limits, high-temperature resistant materials remain at the forefront, bridging innovation and sustainability in a rapidly evolving technological landscape.