February 15, 2025 – Mastering the art of melt flow regulation is pivotal in ensuring the quality and efficiency of TPE (thermoplastic elastomer) pelletizing and product manufacturing processes. So, how can one effectively adjust the melt flow of TPE? Here are some practical tips.
Firstly, tweaking the oil-extended ratio of the base material serves as a fundamental approach to enhancing TPE’s fluidity. Oil extension, a common practice, allows for customization based on the specific characteristics of the base material, such as SEBS or SBS grades, and the performance requirements of the TPE. It’s crucial to strike a balance, however, as excessive oiling may lead to subsequent bleeding of small white oil molecules, compromising material properties.
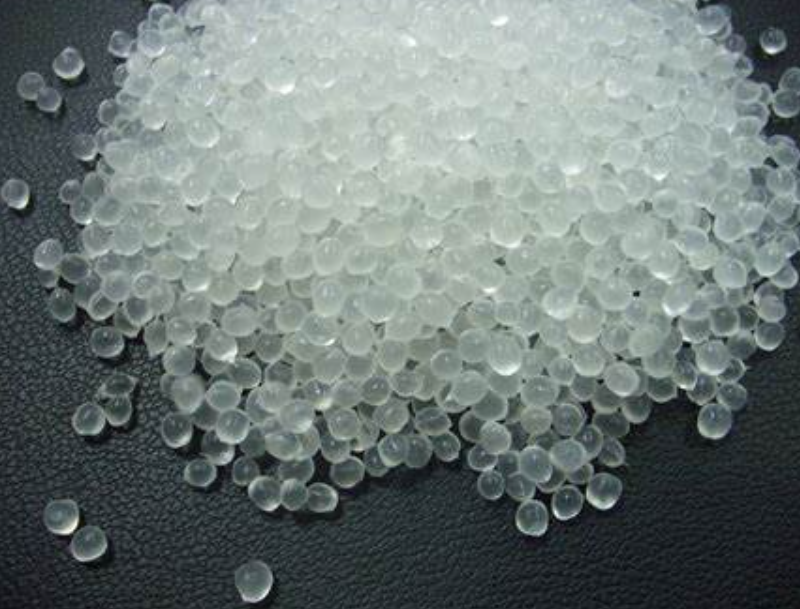
Secondly, adjusting the material formulation plays a vital role in regulating TPE melt flow. The selection of the plastic phase within the TPE formulation is paramount. Opting for high melt flow index PP or PS results in superior melt flow, whereas lower grades decrease it. Furthermore, the type and amount of fillers significantly impact TPE’s fluidity. By optimizing these factors, one can achieve the desired fluidity without compromising material performance. Additionally, the adjustment of lubricants cannot be overlooked. Incorporating appropriate amounts of internal and external lubricants like stearic acid and silicones effectively improves melt flow. However, careful control of these additives is essential to prevent excessive bleeding.
According to AsiaMB’s insights into the color masterbatch industry, processing conditions also offer avenues for adjusting TPE melt flow. For linear SEBS-based materials, screw shear rates primarily regulate fluidity, whereas processing temperatures are more critical for radial SEBS-based counterparts. During this adjustment, vigilant monitoring is required to prevent material degradation or uneven dispersion. Moreover, precise temperature control is vital during product manufacturing. Temperatures that are too high or too low can result in unstable melt flow, necessitating the use of intelligent temperature control systems for real-time monitoring and adjustment. In injection molding, maintaining consistent injection speeds is key to minimizing issues arising from fluidity fluctuations. Increasing injection speeds aids rapid mold filling, while appropriately setting the holding pressure time ensures complete mold filling, reducing defects caused by fluidity variations.