February 24, 2025 – Plastic Automotive Parts Manufacturer Optimizes Material Usage for Sustainable Growth
In the realm of plastic automotive parts production, the management of plastic material consumption is a critical aspect of operational efficiency. From raw material supply to finished product delivery, every step requires meticulous planning to optimize production schedules, reduce costs, and minimize environmental impact. This article delves into the monthly plastic material consumption and optimization strategies employed by a leading plastic automotive parts manufacturer.
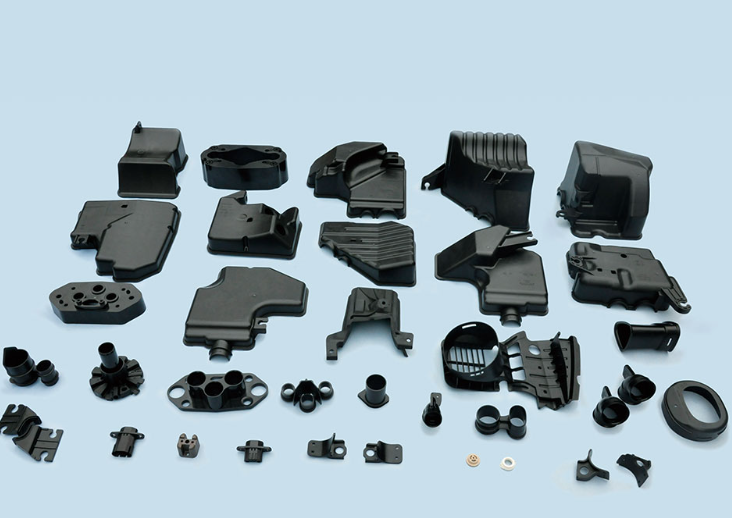
The journey begins with raw material procurement, the foundation of effective plastic material management. The factory primarily utilizes polyethylene (PE) and polypropylene (PP) as its production materials, with a monthly output ranging from hundreds of thousands to millions of pieces. The amount of plastic material used in each finished product varies depending on the type and complexity of the part. Assuming a monthly production of 100,000 units, with body parts accounting for 70% and other components making up the remaining 30%, the factory calculates the exact amount of plastic material required for each product based on density and volume, thereby determining the total monthly consumption.
During the production process, the management of plastic material usage becomes even more precise. Upon arrival, raw materials undergo rigorous quality checks to ensure they meet the required standards. Subsequently, the plastic material is processed through injection molding, extrusion, blow molding, and other forming techniques to achieve the desired shapes. According to industry insights from AsiaMB, the high precision of mold forming results in relatively higher plastic material consumption. Additionally, post-processing tasks such as painting and film application also require additional plastic materials. In the assembly process, the amount of plastic used for joints and seals must be accurately calculated as well.
In terms of quality control, the factory employs automated inspection equipment to ensure product quality and reduce the defect rate. This not only enhances production efficiency but also strengthens the competitiveness of the products. Simultaneously, the adoption of automation technology has reduced labor costs.
On the environmental front, the factory actively implements various measures to minimize plastic material waste and environmental impact. By utilizing eco-friendly chemicals, conserving water and electricity, and recycling by-products, the factory has effectively reduced its plastic material consumption. Furthermore, through optimizing production processes and material formulas, the factory has reduced the over-reliance on plastic materials for certain components, achieving a further reduction in usage.
In conclusion, through precise calculations and optimized management, the plastic automotive parts manufacturer has successfully reduced its monthly plastic material consumption, lowering production costs and minimizing environmental impact. Looking ahead, with continuous technological innovation and management optimization, the factory is poised to embark on a more sustainable development path.