August 22, 2024 – Plastic modification stands as an effective method to enhance plastic performance, improve quality, and reduce costs through the addition of additives and fillers. The role of formula design in this process is pivotal, involving multiple elements such as material selection, compounding, dosage, and mixing methods. These aspects, when combined, significantly impact the final product’s performance.
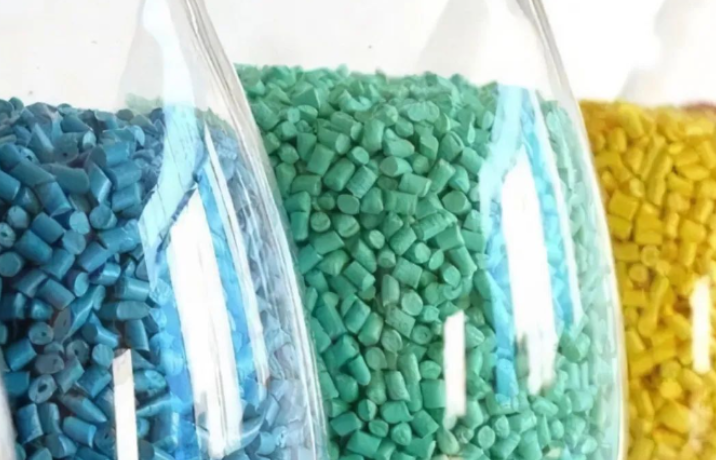
When crafting the formula, resin choice is paramount. It’s crucial to select the appropriate resin type and grade based on the targeted modification. For instance, to bolster resin’s toughness, resins like ABS or SBS may be preferred, while for transparency, PS, PMMA, or PC resins are ideal. Compatibility with the base resin is essential to form a stable composite material.
Besides resin, the selection of additives is equally important. Different additives impart various properties to the plastic, such as flame retardancy, reinforcement, or toughening. When choosing additives, factors like purpose, form, compatibility with the resin, and quantity added must be considered. For example, to enhance the plastic’s flame retardancy, additives like inorganic phosphorus or organic halides can be used, while lubricants like graphite or MoS2 improve wear resistance.
Uniform mixing is a fundamental requirement in plastic formula modification. To ensure additives are evenly distributed in the resin, it’s vital to sequence the addition of fillers logically and introduce large quantities in batches. Additionally, techniques like coupling treatment can enhance additives’ dispersibility and compatibility.
During the formula selection process, factors like processability, fluidity, heat resistance, and environmental friendliness must also be considered. For instance, adding flow modifiers can optimize plastic’s fluidity for better processing. Controlling processing temperatures and incorporating antioxidants is essential to prevent thermal decomposition and ensure additive stability. Furthermore, selected resins and additives should be non-toxic or low-toxic to guarantee the product’s environmental friendliness and human safety.
According to the Color Masterbatch Industry Network, plastic modification technology is continually evolving with technological advancements. In the future, we can expect to see more modified plastic products with exceptional performance, opening up new possibilities for various applications.