July 31st news, Color masterbatch, a pivotal application in the chemical industry, has undergone remarkable progress in recent years. This technology involves the precise formulation of colorants, carrier resins, dispersants, and various additives to produce colored granules with specific concentrations. By incorporating appropriate amounts of these color masterbatches during the product forming process, manufacturers can achieve desired color effects with precision.
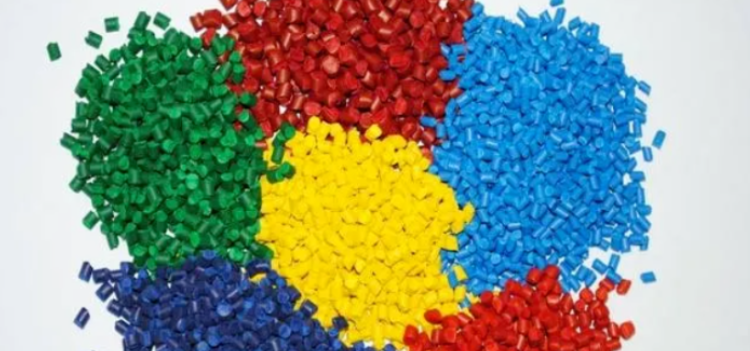
Color masterbatches are classified based on the pre-colored resin, such as ABS, PC, or PP masterbatches. Alternatively, they can be categorized according to the processing technique used for the colored resin, including injection molding, film blowing, and extrusion grades. Pre-processing of pigments in these masterbatches enhances their tinting strength, allowing for reduced usage, consistent quality, facilitated transportation, storage, and application, while minimizing environmental impact.
According to the Color Masterbatch Industry Network, dispersants play a vital role in the production process. These agents wet and penetrate the pigments, eliminating surface air and breaking down aggregates into fine, stable, and uniform particles. For challenging organic pigments and carbon black, EVA wax or oxidized polyethylene wax are employed. It’s worth noting that synthetic low-molecular-weight polyethylene wax differs significantly in performance from that produced via polyethylene pyrolysis.
Moreover, color masterbatches may incorporate various additives like coupling agents, antioxidants, UV stabilizers, antistatic agents, and fillers. The inclusion of these additives, adjusted according to specific needs, endows the masterbatches with multifunctionality. For instance, adding a brightener aids in mold release and enhances the surface gloss of molded products.
When assessing color masterbatch performance, multiple criteria such as color difference, whiteness, yellowness, yellowing index, thermal stability, oxygen index, and melt flow rate are considered. Additionally, pigment fineness, migration resistance, chemical resistance, and toxicity are also relevant factors. In specialized applications, like fiber-grade masterbatches, specific metrics like the filtration value (DF value) become critical.