December 18, 2024 – SABIC Unveils LNP™ ELCRES™ CXL Polycarbonate Copolymer Resin for Enhanced Chemical Resistance
SABIC has recently announced the successful launch of its LNP™ ELCRES™ CXL polycarbonate (PC) copolymer resin, a cutting-edge material that offers novel solutions for customers across the automotive, electronics, industrial, and infrastructure sectors. In the face of escalating challenges from chemical exposure, these specialty materials provide robust protection against environmental stress cracking and premature failure caused by harsh chemicals, ensuring durability and reliability for various components.
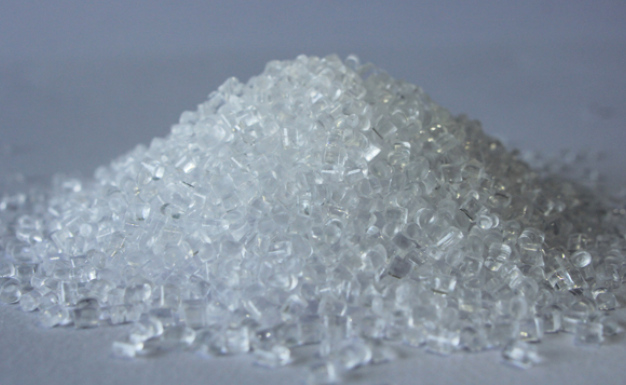
The LNP™ ELCRES™ CXL copolymer resin not only surpasses existing materials in chemical resistance but also boasts exceptional low-temperature impact resistance and weatherability, making its performance in applications even more remarkable. Compared to traditional PC/ABS blends, this new resin demonstrates significant advantages in chemical resistance. Internal tests conducted by SABIC have confirmed that the LNP™ ELCRES™ CXL copolymer resin exhibits strong tolerance to various chemicals, including gasoline, antifreeze, and sodium hydroxide (5% solution), providing reliable material support for applications in transportation, industry, infrastructure, and electronics.
Polycarbonate (PC), as a high-performance polymer, is widely used in electronic appliances, glass assembly, optical discs, automobiles, construction, medical devices, packaging, and more, thanks to its excellent impact resistance, thermal stability, creep resistance, good transparency, electrical insulation, heat resistance, cold resistance, and flame retardancy. SABIC’s introduction of the LNP™ ELCRES™ CXL copolymer resin represents an innovative upgrade to PC materials, meeting the market’s demand for higher chemical resistance.
Moreover, it is worth noting that the production processes for polycarbonate are continuously evolving. Currently, China mainly adopts two methods: interfacial polycondensation with phosgene and non-phosgene melt transesterification. The latter, known for its environmental friendliness, has become the preferred choice for new projects. As a leading player in the chemical industry, SABIC remains committed to material innovation and research, bringing more high-performance, eco-friendly materials to the market.