September 06, 2024 -In the realm of chemical materials, ABS (Acrylonitrile Butadiene Styrene), a celebrated thermoplastic polymer, stands tall due to its exceptional low-temperature impact resistance and lightweight nature, carving a niche across multiple industries. Notably, in the burgeoning 3D printing market, ABS has emerged as a dual giant alongside PLA, both materials dominating the landscape. This comprehensive article delves into the production intricacies, distinctive attributes, 3D printing applications, prominent manufacturers, and market pricing of ABS.
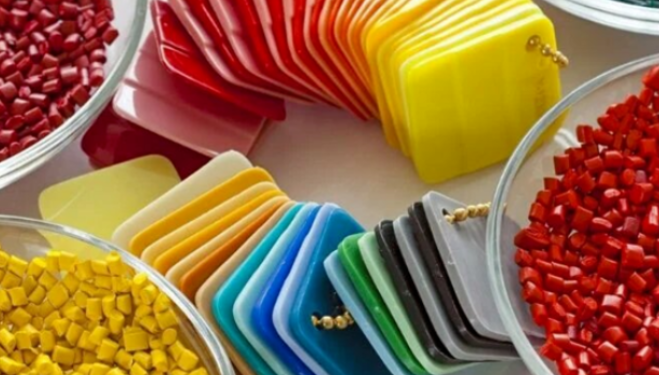
The ternary copolymer known as ABS plastic has been a trailblazer in the industrial 3D printing arena since its inception around 1990. Formed by the intricate blending of acrylonitrile, butadiene, and styrene monomers, ABS offers a versatility in properties tailored by adjusting the monomer ratios. Styrene contributes rigidity and shine, while butadiene bestows exceptional impact resistance and low-temperature tolerance. Intriguingly, despite its petroleum-based origin, contrasting sharply with PLA’s biobased pedigree, ABS’ recyclability grants it an environmental edge. Although acceptance among recycling centers is a work in progress, ABS’ eco-friendliness, when juxtaposed with PLA’s conditional biodegradability, is noteworthy.
Within the 3D printing realm, ABS is prevalently utilized in filament form, commonly available in 1.75mm or 2.85mm diameters, offering a palette of hues. Despite posing slightly greater printing challenges than PLA, ABS’ resilience to impacts and temperature fluctuations (-20°C to 80°C) renders it a preferred choice for professional 3D printing endeavors. Its opacity, coupled with a sleek, glossy surface, adds depth to printed creations. However, ABS’ propensity for warping necessitates the use of heated print beds (80-130°C) and enclosed 3D printers to ensure successful prints. Moreover, sensitivity to humidity necessitates dry storage to avoid printing difficulties.
According to AsiaMB’s insights, ABS plastic’s 3D printing applications span from prototype design to industrial components like gears and molds, extending to electrical parts and automotive exteriors, showcasing its technological prowess. Its chemical resistance, heat tolerance, and electrical insulation make it an ideal candidate for outdoor and electrical applications. Furthermore, enhancing its appeal, ABS can undergo acetone vapor smoothing, yielding an even smoother surface, elevating its application value.
The market boasts a plethora of ABS filament manufacturers, including renowned brands such as Stratasys, Esun, UltiMaker, FormFutura, and Innofil3D. Prices vary by brand, ranging from 15 to 60 euros. Catering to premium demands, the market also offers ABS filaments infused with carbon fibers or aramid fibers, mitigating warping and elevating print precision and mechanical properties.
In conclusion, ABS plastic, with its distinctive properties and vast application spectrum, remains a cornerstone in the chemical materials and 3D printing industries. As technology advances and market boundaries expand, the future of ABS plastic promises to be both promising and dynamic.