January 24, 2025 – Plastic coloring is an indispensable aspect of plastic processing, and the choice of colorants directly affects the final outcome of plastic products. Today, we delve into the world of plastic colorants, particularly focusing on four common types: color powder, color masterbatch, color paste, and color oil. By examining their respective advantages and disadvantages, we aim to assist you in making better choices for injection molding or other plastic processing methods.
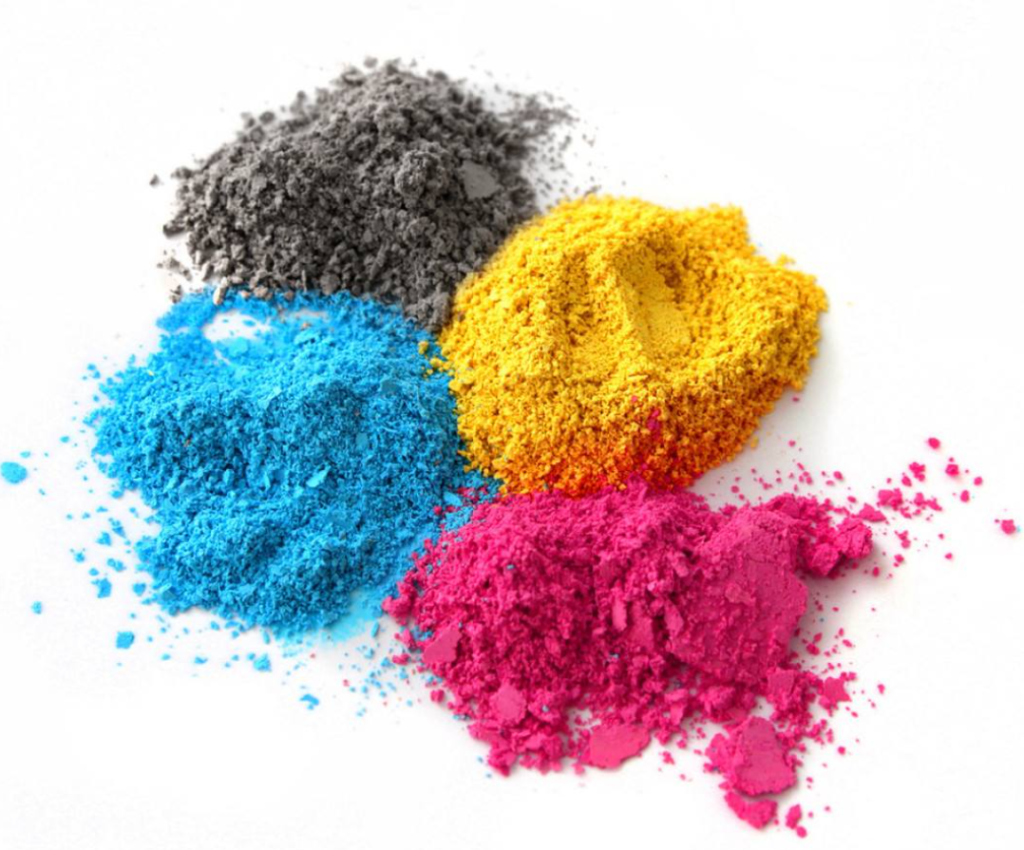
Starting with color powder, this method involves directly adding pigments or dyes in powder form to plastic particles. It is straightforward and relatively low in cost, offering excellent dispersion, especially suitable for small-batch plastic processing. However, it has notable drawbacks such as dust pollution that can impact the work environment. Cleaning the hopper when changing colors is also a challenge. Additionally, for products like blown film and spun yarn, color powder may not be reliable as the pigment powder may not fully bond with the resin, leading to incomplete coloring.
Moving on to color masterbatch, this involves mixing pigments into a carrier resin to create particles similar in size to resin grains. This solution addresses the issue of dust flying and facilitates easier color changes. Color masterbatch offers targeted coloring, simple color matching, and easy quantification. However, it may have poorer dispersion and higher costs. If the carrier in the color masterbatch differs in properties from the resin being colored, the plastic product’s surface may exhibit undispersed spots, color patches, or streaks.
Color paste is another option, consisting of pigments and fillers dispersed in a binder. It is convenient to use, exhibits good high-temperature resistance, and is easy to store. Color paste reduces dust pollution associated with color powder use and allows for easy control of the input quantity, minimizing color differences and enhancing color strength and brightness. However, high-quality color paste demands rigorous processing and raw material quality, leading to potentially higher costs than color masterbatch or color powder. Excessive addition may cause screw slipping, and prolonged storage can result in sedimentation.
Lastly, we have color oil, a concentrated liquid pigment without a resin carrier. Color oil boasts low addition rates for effective coloring, excellent dispersion, and highly uniform and vibrant colors. It maintains the physical properties of the base resin through a single high-temperature process. Color oil is also convenient to store, saving warehouse space, and simplifies color changes. However, color oil cannot incorporate antistatic agents, making dust prevention during shelf or storage impossible. Additionally, color oil products have a shorter shelf life compared to color masterbatch. Moreover, specialized equipment is required to supply color oil to injection molding machines for producing colored products.
According to AsiaMB, when selecting plastic colorants, it is crucial to consider product usage requirements, processing conditions, costs, and environmental factors comprehensively. Only by fully understanding the pros and cons of each colorant can one make the most suitable choice, ensuring plastic products achieve optimal results.