September 13, 2024 – Polypropylene (PP), a staple in the production of plastic goods across home appliances, packaging, and medical sectors, has faced limitations due to its low-temperature brittleness. To overcome this challenge, chemical industry researchers have embarked on incorporating ABS blend modification toughening agents into PP composite systems. The aim is to enhance the material’s impact resistance and anti-aging properties while maintaining its ease of processing.
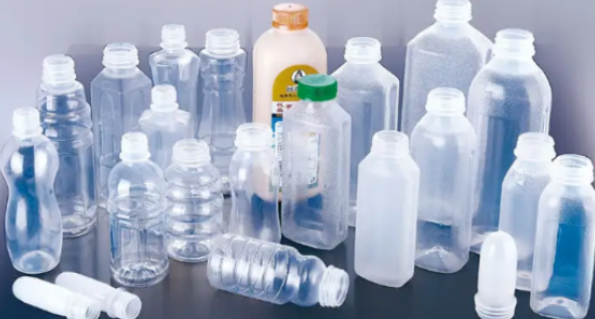
In the realm of PP/SBS blend modification, researchers have primarily adopted two methodologies: copolymer blend modification and physical blending. The copolymer blend modification encompasses techniques such as graft copolymerization-blending and block copolymerization-blending, which modify filler surfaces through chemical reactions or adsorption. Physical blending, on the other hand, includes powder blending, melt blending, solution blending, and emulsion blending. For instance, powder blending involves uniformly mixing two or more fine polymer powders in a mixing device, optionally with the addition of antioxidants, coupling agents, and other plastic additives.
According to Color Masterbatch Industry Network insights, researchers devised two experimental protocols to validate the modification effects. The first protocol involved directly blending PP, SBS, and SEPS (2% by weight) and processing them through twin-screw extrusion, pelletizing, drying, and injection molding to obtain test samples. The second protocol employed a two-stage blending method, where SBS, SEPS, and a portion of PP were initially blended to form a sea-sea structure, followed by mixing with the remaining PP to yield the final samples.
The experimental results underscored the significant impact of SBS content on the blend’s properties. At 15% SBS content, the tensile strength reached its peak; however, beyond this threshold, the tensile strength gradually declined. Similarly, prior to 15% SBS content, the composite’s elongation at break increased with SBS content, but it decreased subsequently. Notably, the properties of composites from the second protocol outperformed those from the first, attributed to more uniform mixing.
Regarding melt flow index, as SBS content rose, the composite’s melt flow index significantly decreased. This was mainly due to SBS’s lower melt flow index and the formation of a macromolecular chain-like relationship between PP and SBS facilitated by the compatibilizer SEPS, which increased the blend’s viscosity and reduced its fluidity.
Impact strength tests also revealed that SBS addition markedly improved the composite’s impact strength. As SBS content increased from 0 to 25%, the impact strength of samples from both protocols nearly tripled. Furthermore, spherulite experiments elucidated SBS’s disruptive effect on PP spherulite morphology, which was the fundamental reason for the enhanced impact performance.
In conclusion, PP/ABS blend modification not only effectively addresses the low-temperature brittleness of PP products but also leverages the respective advantages of PP and ABS. This provides robust support for broadening PP’s application scope, reducing costs, and enhancing environmental protection and sustainability.