July 21, 2025 –
Material Showdown: Understanding the HDPE vs. PE Pipe Selection Dilemma
The piping industry continues to witness growing specialization between HDPE and conventional PE materials, with each demonstrating distinct advantages for different industrial applications. Recent market analysis reveals these polymer alternatives are carving out separate but equally vital roles in modern infrastructure projects.
HDPE’s superior molecular density (0.941-0.965g/cm³) translates to exceptional pressure resistance, making it the undisputed choice for critical gas distribution networks. “The material’s structural integrity under stress explains its dominance in municipal gas systems,” notes an AsiaMB technical consultant. Meanwhile, standard PE pipes (0.910-0.925g/cm³) maintain strong market presence due to their cost-effectiveness and adaptability across multiple fluid transfer applications.
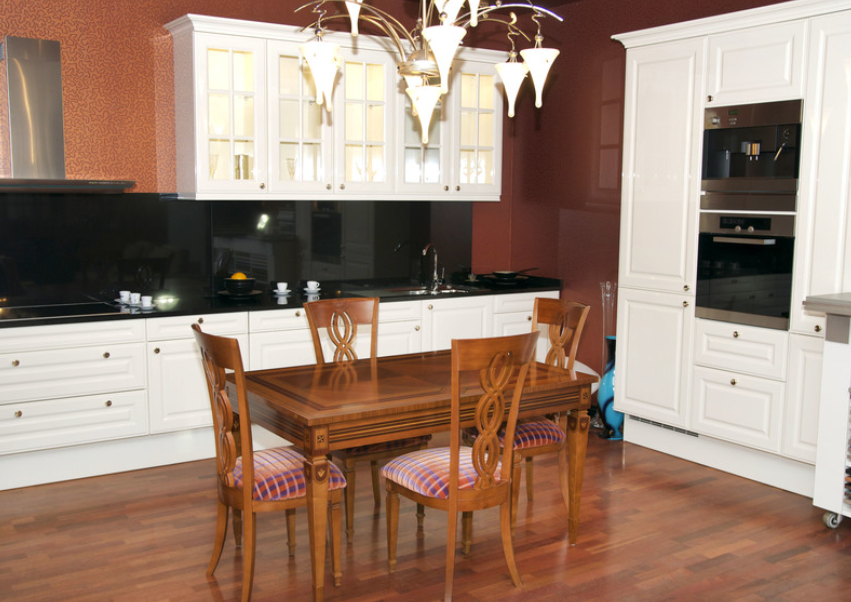
Industry professionals highlight several key selection criteria:
• Pressure requirements (HDPE excels in high-pressure scenarios)
• Chemical compatibility (both resist corrosion but differ in permeability)
• Installation flexibility (PE offers better bending radius)
• Lifecycle costs (HDPE’s durability offsets higher initial investment)
The residential sector presents additional considerations, where PE-XC and PPR pipes have gained traction for potable water and heating systems respectively. “Modern construction projects often combine multiple pipe types,” explains a project engineer. “We might use HDPE for underground gas lines, PE for drainage, and specialized polymers for interior plumbing.”
Material scientists emphasize that ongoing polymer innovations continue to blur traditional performance boundaries. Recent HDPE formulations now challenge PE’s flexibility advantages, while new PE composites demonstrate improved pressure ratings. This technological evolution requires specifiers to regularly update their material selection protocols.