July 20, 2025 –
Breakthroughs in Wear-Resistant PA6 Technologies Open New Application Frontiers
Recent advancements in polyamide 6 (PA6) modification technologies are revolutionizing the engineering plastics sector, with researchers achieving remarkable improvements in wear resistance through innovative blending and reinforcement techniques.
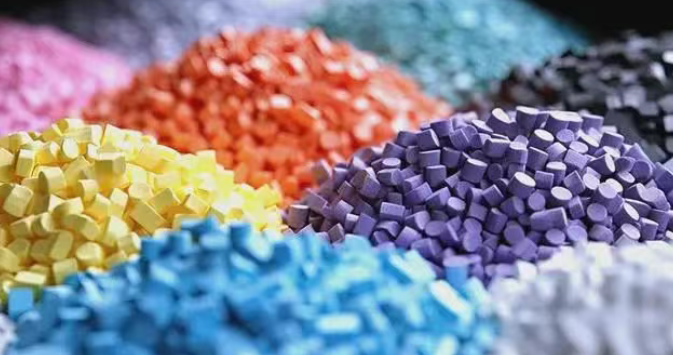
The materials science community has made significant progress in polymer blending approaches. Industry tests reveal that:
• A 5% ABS blend reduces PA6 wear rates to 92μm
• HDPE blends in 6:4 ratios decrease friction coefficients by over 70%
• PTFE additives at 10% concentration lower friction by 32% while cutting wear rates by 28%
Fiber reinforcement methods have demonstrated even more dramatic enhancements:
✓ Basalt fiber incorporation (10%) achieves 95% wear reduction
✓ Carbon fiber loading (20%) slashes friction coefficients by 57.7%
✓ Continuous carbon fiber composites achieve ultra-low directional wear rates of 2.31×10⁻⁶mm³/(N・m)
Perhaps most promising are the synergistic effects discovered in hybrid modification systems. The combination of 33% glass fiber with 5% molybdenum disulfide produces:
→ 18.84% additional wear reduction compared to single-filler systems
→ 24.8% improvement in surface roughness
→ Optimal balance between rigidity and flexibility
“These technological leaps address PA6’s historical limitations while unlocking new performance capabilities,” commented Dr. Elena Rodriguez, materials scientist at the Advanced Polymers Research Institute. “The precision-engineered modifications we’re seeing today will enable PA6 to compete in applications previously dominated by specialty alloys.”
Industry analysts predict these developments will accelerate PA6 adoption in demanding sectors like automotive components, industrial machinery, and high-performance bearings, potentially reshaping the engineering plastics market landscape in coming years.