August 14, 2024 – The journey of fluoroplastics began in 1934 when I.G. Farbenindustrie in Germany, through the collaborative efforts of F. Schloffer and O. Scherer, developed polychlorotrifluoroethylene (PCTFE), marking the birth of fluoroplastics. Just four years later, in 1938, Dr. Plunkett from DuPont pushed the boundaries further by inventing polytetrafluoroethylene (PTFE), paving the way for new research and applications in fluoropolymer-based materials.
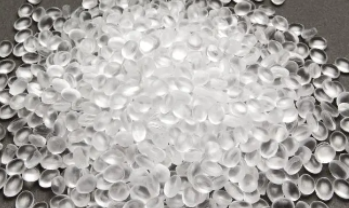
As technology progressed and market demands grew, various fluoroplastics emerged. In 1955, vinylidene fluoride-chlorotrifluoroethylene copolymer (VDF-CTFE) was successfully developed. Around 1960, polyvinyl fluoride (PVF), polyvinylidene fluoride (PVDF), and ethylene-chlorotrifluoroethylene copolymer (ECTFE) followed suit. The 1970s witnessed the creation of novel fluoroplastics such as perfluorosulfonic acid resin (XR resin), tetrafluoroethylene-hexafluoropropylene copolymer (FEP), ethylene-tetrafluoroethylene copolymer (ETFE), and tetrafluoroethylene-perfluoroalkyl vinyl ether copolymer (PFA).
Fluoroplastics, enriched with fluorine atoms, exhibit remarkable properties like excellent flame retardancy, stability, electrical insulation, mechanical strength, and heat resistance. Additionally, they possess superior oil, solvent, abrasion, moisture, and low-temperature resistance. These unique physical and chemical characteristics have led to their widespread use in high-tech industries like defense, aerospace, semiconductors, and electronics, as well as traditional sectors like construction, healthcare, and automotive.
Among the various fluoroplastics, PTFE stands out due to its extraordinary features. This polymer, derived from tetrafluoroethylene, demonstrates exceptional cold resistance, maintaining its mechanical toughness even at -196℃. Its corrosion resistance is outstanding, showing inertness to most chemicals and solvents. PTFE’s difficulty in being wetted allows it to retain its original weight and dimensions after prolonged soaking in water. Furthermore, its lubricity, low friction coefficient, and excellent dielectric properties make it a top choice for electrical insulation applications.
Interestingly, during World War II, PTFE was considered a crucial military supply owing to its distinctive qualities. With the chemical industry’s evolution, PTFE has emerged as one of the most produced and rapidly growing fluororesins. In everyday life, PTFE finds its place in non-stick cookware coatings and outdoor jacket fabrics. The PTFE membrane technology in outdoor jackets offers a perfect balance of waterproofing and breathability, enhancing comfort during outdoor activities. Besides, PTFE is extensively used in specialty protective clothing, footwear, and industrial smoke filtration.