August 12, 2024 – Polyphenylene ether, commonly known as PPE or PPO, stands out as the lightest engineering plastic, garnering attention for its exceptional dimensional stability and inherent halogen-free flame retardant properties. This versatile material has found its place in various sectors, including photovoltaics, automotive, electronics, home appliances, and water treatment. Notably, this innovative plastic, invented by the renowned General Electric, ranks among the world’s top five general-purpose engineering plastics.
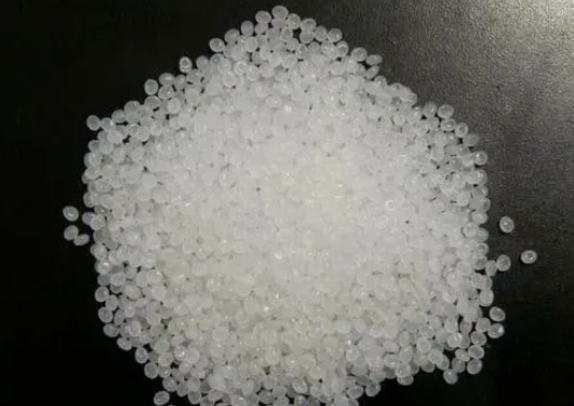
Polyphenylene ether excels in its comprehensive performance, making it ideal for manufacturing heat-resistant, insulating, wear-reducing, and transmission components, as well as medical and electronic parts. It can withstand high temperatures, serving as gears, fan blades, valves, and even as a substitute for stainless steel. Additionally, it’s utilized in creating screws, fasteners, connectors, motor rotors, and transformer parts.
In the photovoltaic industry, polyphenylene ether plays a pivotal role. Solar panels generate voltages lower than required, necessitating the combination of multiple panels via photovoltaic connectors to achieve the desired voltage and current. These connectors demand high reliability to withstand various environmental conditions, safety standards, and longevity. Polyphenylene ether, with its superior properties like high temperature resistance, flame retardancy, UV resistance, and low water absorption, emerges as the perfect material for photovoltaic connector housings.
Technological advancements continue to expand the application areas of polyphenylene ether. Modified versions of this plastic are now widely used in the production of televisions, photocopiers, and video cameras. Researchers are also addressing its limitations, such as water absorption, to enhance its performance further.
Global consumption of polyphenylene ether is increasing annually, with a growing presence in the automotive sector. Despite its status as one of the top five engineering plastics, there’s still room for improvement in its production and consumption in China. As the automotive industry moves towards lightweight vehicles and carbon neutrality goals, polyphenylene ether’s advantages become more prominent, paving the way for a more significant role in the automotive and photovoltaic materials sectors.
Currently, only five companies worldwide have mastered the industrial production technology of polyphenylene ether at the 10,000-ton level. Among them are China National Bluestar (Group) Co., Ltd. and Xinbao New Materials Co., Ltd. In recent years, Nantong Xingchen Synthetic Materials Co., Ltd., a subsidiary of China Bluestar, has made remarkable progress in polyphenylene ether production, solidifying China’s leading position in the global polyphenylene ether industry.