August 10, 2024 – PPS, a high-performance specialty engineering plastic, has garnered significant attention due to its unique chemical structure that maintains stability under high-temperature environments. The conjugated structure of benzene rings and sulfur atoms in its main chain prevents PPS from decomposing or undergoing crosslinking reactions at high temperatures, ensuring that the material’s physical and chemical properties remain unaffected in extreme heat. This characteristic gives PPS a notable advantage in the field of film production.
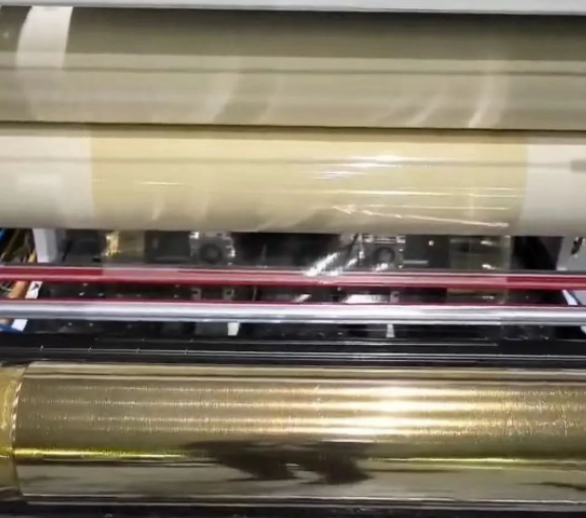
PPS cast film is a non-oriented flat-extruded film made by rapidly cooling molten PPS resin. The production process involves various steps, including ingredient preparation, melt extrusion, casting, forming, cooling, traction, trimming, and rewinding. The resulting PPS film boasts a smooth surface with a thickness that can reach several micrometers, while maintaining its performance.
According to the Color Masterbatch Industry Network, PPS film has seen significant development both domestically and internationally. Many domestic manufacturers have completed technical explorations and achieved a certain scale of production capacity. The film width has expanded from 300mm to 1200mm, and some have even reached 2.4m with mass production, fully leveraging the advantages of PPS as a functional plastic and breaking through technical and production barriers in China’s high-performance engineering plastic industry. Overseas, major manufacturers like Toray and Teijin in Japan, and SKC Kolon in Korea, have produced PPS films with a minimum thickness of 2μm, providing inspiration and momentum for the development of China’s plastics industry.
PPS film, with its exceptional properties, has demonstrated advantages in multiple fields. Its heat resistance and corrosion resistance allow it to maintain stable performance at temperatures up to 220℃, and its mechanical properties remain unchanged even at extremely low liquid helium temperatures. Additionally, PPS film offers excellent flame retardancy, acid and alkali corrosion resistance, and low water absorption, making it widely used in electrolytic cells, diaphragms, capacitors, and other applications. It particularly excels in film capacitors.
Furthermore, the dielectric properties of PPS film are comparable to or even better than LCP film, making it a suitable substitute for LCP film in flexible printed circuit boards (FPC), which are essential components in 5G technology. This gives PPS film vast potential in the 5G sector.
Compared to PET polyester film, PPS film is more heat-resistant, flame-retardant, moisture-resistant, and hydrolysis-resistant. When compared to polyimide PI film, PPS film offers a lower cost and more accessible raw materials. Moreover, PPS film has a moderate surface tension, suitable for coating processes, and its surface roughness and friction coefficient can be adjusted based on the application. Remarkably, PPS film exhibits high durability against r-rays and neutron radiation, making it one of the few organic films suitable for use in atomic reactors and nuclear fusion furnace peripheries.
As societal demand for plastic materials continues to grow and application requirements increase, PPS plastics and their derivatives are finding wider use in various fields. The future is expected to bring further improvements in PPS film preparation techniques and quality, enhancing the competitiveness of China’s new material products in the international market.