April 27, 2025 – In the current wave of technological advancements, the humanoid robot sector is experiencing rapid growth, and the associated material technologies have captured significant attention. Recently, XPENG Motors unveiled its humanoid robot IRON at the Shanghai Auto Show, announcing plans for large – scale industrial mass production by 2026, which has sparked widespread interest across the industry. Meanwhile, Elon Musk revealed that thousands of Optimus robots are expected to be deployed in factories in 2025, with the ambitious goal of producing one million units annually by 2029 – 2030. These strategic moves by industry giants have painted a promising future for humanoid robots.
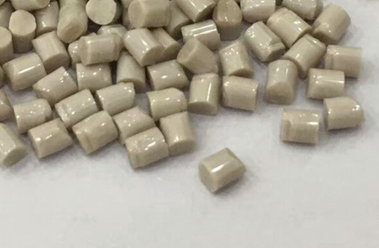
Against this backdrop, PEEK (polyetheretherketone), a high – performance special engineering plastic, has emerged as a key player due to its outstanding properties, showcasing great potential in the humanoid robot field. Domestic humanoid robot companies have already started using PEEK lightweight materials, and there is a strong likelihood of its widespread application in the future. Take Tesla’s Optimus Gen2 as an example. Behind its 10kg weight reduction “black technology”, PEEK materials, with a specific strength eight times that of aluminum alloy, along with their lightweight and high – temperature resistance features, have become a game – changing alternative to traditional metal materials. Currently, PEEK is being used in its linear actuators.
According to AsiaMB, the advantages of PEEK materials suggest their continuous penetration across multiple aspects of humanoid robots. In motors, PEEK can be applied to rotor sleeves, film motor slots, and enameled wires, providing insulation while ensuring good heat dissipation. In the bearing field, PEEK bearing cages can replace metal or nylon materials, effectively solving the problem of fretting wear during high – speed operation. For instance, PEEK – graphene composite bearings were once used in Boston Dynamics’ Atlas’ metacarpophalangeal joints, significantly reducing friction losses. In reducers, harmonic reducers made of carbon fiber – reinforced PEEK (CF/PEEK) can reduce the friction coefficient to 0.05, extend the service life by three times, and are compatible with the “elastic hollow roller + polymer bearing” structure, achieving a weight reduction of 30% – 50%. In the future, for shell manufacturing, PEEK can be used in injection molding processes to achieve complex topology optimization designs. Drawing from the example of DJI drones, which achieved a 58% weight reduction compared to aluminum alloy by using PEEK composite skeletal frames, the application of PEEK in humanoid robot shells holds great promise. It is estimated that the value of PEEK materials per humanoid robot could rise to nearly 10,000 yuan, opening up a market worth over 100 billion yuan.
PEEK materials have a wide range of applications across various fields, including automotive, medical, aerospace, electronics, 3D printing, and robotics. Specifically, the automotive sector accounts for 30% – 40% of its usage, the information sector about 30% – 40%, and the industrial field 20% – 30%. Looking at the consumption growth trend, global PEEK consumption increased from 3,590 tons in 2012 to 5,835 tons in 2019, with an average annual growth rate of 7.2%. According to GrandView Research, the global PEEK market size was estimated at 799 million US dollars in 2023 and is projected to grow at a compound annual growth rate of 8.0% from 2024 to 2030. With the trends of “replacing steel with plastic” and “lightweighting”, PEEK, with its inherent advantages, is gradually replacing metals in mid – to high – end applications, and humanoid robots are expected to be one of the fastest – growing application areas.
In China’s A – share market, numerous companies are actively involved in the PEEK material field. Zhongxin Fluoride Materials ranks first in A – share fluoroketone production capacity. With its globally leading fluoroketone production capacity, it has entered Tesla’s humanoid robot supply chain as a core raw material supplier. The company’s 5,000 – ton – per – year fluoroketone production capacity has been steadily put into operation, and its high – purity DFBP products, a key raw material for PEEK materials, have successfully passed Tesla’s Tier1 certification in Hangzhou, seizing the opportunity for domestic substitution. As the global demand for lightweighting surges, it is expected to advance further with its technological, production capacity, and cost advantages. Zhongyan Co., Ltd. is the largest PEEK manufacturer in China and ranks among the top four globally, with a global market share of 8.07%. It is the fourth company globally to achieve an annual PEEK production capacity of over 1,000 tons and the second globally to use a 5,000L reactor for PEEK polymerization production. Currently, it has an annual production capacity of 1,000 tons of PEEK and has established a comprehensive product system.
In addition to the above – mentioned companies, many other related enterprises have their own layouts in the PEEK material field. In terms of PEEK products, Wotefu Group is in the process of building a PEEK production line; Kaisheng New Materials has a PEEK production capacity of 1,000 tons per year, offering substitute PEEK products; Shuangyi Technology possesses 3D – printed PEEK – CF composite materials; Kangtuo Medical is the first domestic manufacturer to obtain a registration certificate for PEEK cranial repair products; Tongyi Co., Ltd. has achieved full – category coverage and can mass – produce special plastics such as PEEK, PPS, and PEI; Zhaomin Technology has rich experience in the field of special engineering plastics; Kent Co., Ltd. has developed PEEK anti – wear and high – temperature resistant products; Kingfa Sci. & Tech. Co., Ltd. has the ability to independently research, produce, and polymerize PEEK, and its products have entered the supply chain of high – end robots. In the PEEK fluoroketone raw material segment, Xinhang New Materials ranks second in A – share fluoroketone production capacity, reaching 3,400 tons, and its DFBP products are core raw materials for downstream PEEK production. In the hydroquinone field, Zhejiang Longsheng holds the largest domestic market share, while Brother Technology mainly sells its products to domestic mainstream acrylic acid manufacturers. In the sodium carbonate field, China National Salt Industry Corporation, Sanyou Chemical, and Shandong Haihua rank among the top three in domestic production capacity. The fluorobenzene products of Fujian Shunyue, a subsidiary of Dayang Biotech, are key raw materials for DFBP, an intermediate of PEEK materials. As a leading domestic DFBP manufacturer, it can meet the needs of over 60% of domestic PEEK enterprises. With the rapid development of the humanoid robot industry, these companies are expected to embrace new opportunities in the PEEK material market, driving the entire industry forward.