April 24, 2025 – Since DuPont successfully invented nylon (polyamide, PA) in 1938, this polymer material centered around amide bonds has embarked on a remarkable development journey. Starting as a material for stockings, nylon has transformed into an indispensable “backbone” of modern industry. Thanks to its outstanding properties such as high strength and wear resistance, nylon has made a stunning transition across various sectors including automotive, electronics, and healthcare. In 2024, the global production capacity of nylon exceeded 10 million tons, and the compound annual growth rate of China’s consumption market reached 7.5%. Its application boundaries are continuously expanding into cutting – edge fields like new energy and biomedical technology.
Today, nylon has long broken free from traditional application limitations and emerged as a versatile material across multiple industries. It drives the lightweight revolution in the automotive sector, enables breakthroughs in precision medicine in the biomedical field, and supports the precise operation of industrial robots. The nylon industry encompasses a vast family of products, with five major types including nylon 6 and nylon 66, as well as various copolymer – modified variants. Among them, nylon 6 and nylon 66 account for up to 90% of total nylon consumption and are widely used in both civil and industrial downstream applications. According to AsiaMB, with continuous technological innovation and industrial upgrading, nylon materials are set to embrace an even broader development space.
In the wave of automotive lightweighting, nylon materials play a pivotal role. As China’s automotive industry thrives, the demand for engineering plastics in vehicles has skyrocketed, and PA materials have stood out due to their excellent performance. It is predicted that the sales volume of new energy vehicles in China will reach 7 – 9 million units in 2025 and climb to 17 – 19 million units by 2030. By then, the consumption of PA materials in vehicles will reach 1.44 million tons. Around the engine, nylon has replaced traditional metals in manufacturing components such as intake manifolds and oil pans, significantly reducing weight, cutting costs, and improving fuel efficiency. In the new energy vehicle segment, nylon truly shines. From battery pack casings to heat management system pipelines, its advantages of low density, high strength, and excellent oil resistance are fully utilized, promoting vehicle weight reduction and efficiency enhancement. Meanwhile, the industry has been constantly exploring innovative solutions to overcome technical challenges such as high – temperature resistance, weather resistance, and recycling.
The biomedical field is also a crucial application area for nylon materials. Due to its structural similarity to human proteins, PA materials exhibit excellent biocompatibility. Since the 1970s, they have been widely used in various medical products such as surgical sutures, catheters, and denture bases. Whether as non – absorbable high – strength sutures or for manufacturing medical catheters and balloons, PA materials demonstrate unique advantages. Additionally, innovative applications like antibacterial PA materials, 3D – printed PA medical devices, and bone growth scaffolds are continuously expanding the boundaries of nylon’s use in the medical field.
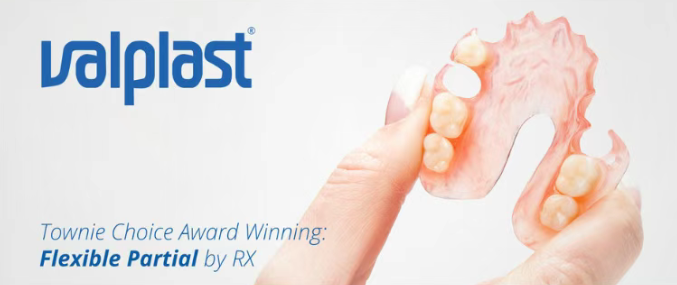
In industrial robot manufacturing, PA6 and PA66 have become ideal structural materials due to their lightweight, wear – resistant, and tough characteristics. From gears in harmonic reducers to the skeletons of flexible actuators, nylon materials enable robots to perform precise movements and flexible operations. With the development of the robotics industry, nylon materials are expected to create a virtuous cycle of “quantity driving technology,” accelerating the localization process of special nylon and promoting the research and innovation of specialized modified nylon.
Currently, the nylon industry is undergoing technological transfer and ecological reconstruction through cross – industry integration. Collaborative innovation along the entire industrial chain, from raw material production to end – use applications, has led to continuous breakthroughs. Upgrades in material properties and processing technologies have given rise to a continuous stream of new technologies, such as ultra – high – performance nylon and intelligent responsive materials. Nylon is also pushing the limits in special fields like deep – sea exploration, space exploration, and nuclear energy. At the same time, the concepts of circular economy and biological manufacturing are taking root, and green products like recycled nylon and bio – based nylon are injecting new impetus into the sustainable development of the industry. From automobiles to healthcare, from the earth to space, nylon materials are redefining the future of materials science with their infinite possibilities.