April 8, 2025 – In the vast realm of chemical material applications, achieving a high – gloss surface is of utmost significance for plastic and TPE products. Different types of materials have their own unique high – gloss solutions.
There are distinct differences in the application fields of plastic high – gloss agents and TPE high – gloss agents. Plastic high – gloss agents are mostly used in hard components that require a high – gloss finish. In the home appliance sector, for items such as TV panels, air conditioner casings, and washing machine control panels, materials like ABS and PP are often used in combination with plastic high – gloss agents to enhance surface luster. In automotive parts, interior panels, instrument panels, and headlamp covers made of PC/ABS and PP materials also rely on plastic high – gloss agents to present a high – quality appearance. In the field of electronic products, mobile phone casings, laptop computer casings, and LED lamp covers, which are commonly made of PC and PMMA materials, are paired with plastic high – gloss agents. In packaging materials, cosmetic bottles, food containers, and transparent blister packaging made of PET and PS materials also need plastic high – gloss agents to add luster.
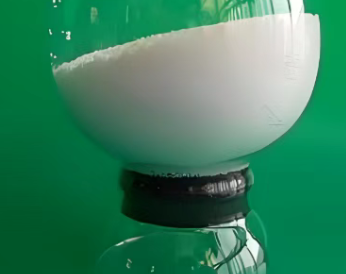
On the other hand, TPE high – gloss agents focus on elastomeric materials, not only emphasizing surface aesthetics but also taking into account functionality such as anti – stick and stain – resistance. In the consumer electronics field, smartwatch straps, headphone cables, and mobile phone cases made of SEBS – based TPE require TPE high – gloss agents to optimize their appearance. In automotive accessories, steering wheel coverings and door seals made of TPV and TPU materials not only need a high – gloss effect but also require wear resistance. In medical supplies, the surfaces of infusion tubes and breathing masks made of medical – grade TPE, while being biocompatible, need TPE high – gloss agents to enhance surface texture. In kitchen and bathroom products, soft TPE products such as anti – slip mats and shower hoses, which require water resistance and easy cleaning, rely significantly on TPE high – gloss agents. In sports equipment, yoga mats and grip covers made of TPE/TPU materials require a combination of high gloss and anti – slip performance, for which TPE high – gloss agents play a crucial role.
According to AsiaMB, there is a wide variety of commonly used plastic surface high – gloss agents. Among wax – based high – gloss agents, polyethylene wax (PE wax) can effectively improve luster and reduce friction, and is widely used in materials such as PP and ABS. Oxidized polyethylene wax (OPE wax) has a remarkable effect on enhancing the compatibility of polar plastics such as PVC and PC. Polytetrafluoroethylene wax (PTFE wax) is heat – resistant and suitable for engineering plastics such as PA and POM. Among fatty acids and their derivatives, zinc stearate/calcium stearate are cost – effective and have both lubricating and brightening effects, being commonly used in general – purpose plastics. Ethylene bis – stearamide (EBS) can improve surface smoothness and luster and reduce exudation. For silicone – based agents, silicone oil/silicone resin can significantly enhance luster, but attention should be paid to the dosage during use, otherwise, it may affect subsequent spraying or bonding. Silicone masterbatch exists in a pre – dispersed form, which can reduce the risk of migration. Special polymers such as PMMA (polymethyl methacrylate) microspheres can enhance light reflection by filling surface micro – defects and are suitable for transparent plastics. Acrylate – based brighteners can improve surface smoothness and reduce haze. Among nanomaterials, nano – silica/nano – alumina can fill surface micro – pores and improve the mirror effect.
For TPE, due to its tendency to be sticky or matte, special high – gloss agents are required. Common ones include silicone – based agents. Liquid silicone oil can improve smoothness and luster when directly blended, but there is a migration problem. Silicone masterbatch is more stable and reduces exudation. Fluorine – based additives such as fluorinated ethylene – propylene copolymer (FEP) have an extremely low surface energy and can provide a long – lasting high – gloss effect, being suitable for high – demand TPE products. Amide – based lubricants such as erucamide/oleamide can reduce surface friction and enhance luster, being suitable for soft TPE. Maleic anhydride – grafted polymer PP – g – MAH can enhance compatibility with TPE and reduce exudation. Special fillers such as ultra – fine talc/glass microspheres can indirectly improve luster through surface flattening.
In TPE applications, the relationship between external lubricants and high – gloss agents is also worthy of attention. The main function of external lubricants is to reduce the friction between the melt and the mold and improve demolding, such as stearic acid and paraffin. High – gloss agents are mainly used to enhance surface luster, and some high – gloss agents also have lubricating effects, such as silicone oil and PMMA microspheres. In practical applications, there is a synergistic effect between the two. Some high – gloss agents such as silicone oil and amides can reduce the amount of external lubricants used. However, there are also potential conflicts. Excessive external lubricants such as zinc stearate may exude, causing surface whitening and reducing luster. If the high – gloss agent has too strong a migration property, such as liquid silicone oil, it may affect subsequent spraying or bonding. Therefore, in practical applications, it is recommended to give priority to multi – functional additives such as silicone masterbatch, which can both brighten and lubricate. Control the dosage of external lubricants, generally not exceeding 0.5%, to avoid affecting luster. At the same time, test compatibility through a thermal aging test (70℃×48h) to observe whether there is any exudation.