March 21, 2025 – A recent research report by Sinolink Securities highlights that the current PET recycling industry is primarily dominated by physical methods, with a relatively mature industrial chain and processes. However, as market demand continues to surge, chemical methods are gradually emerging as a significant development direction for the future of PET recycling. In China, only a handful of companies are currently involved in chemical PET recycling. Therefore, those enterprises that can achieve large-scale and cost-effective production are poised to gain a competitive edge in the fierce market competition.
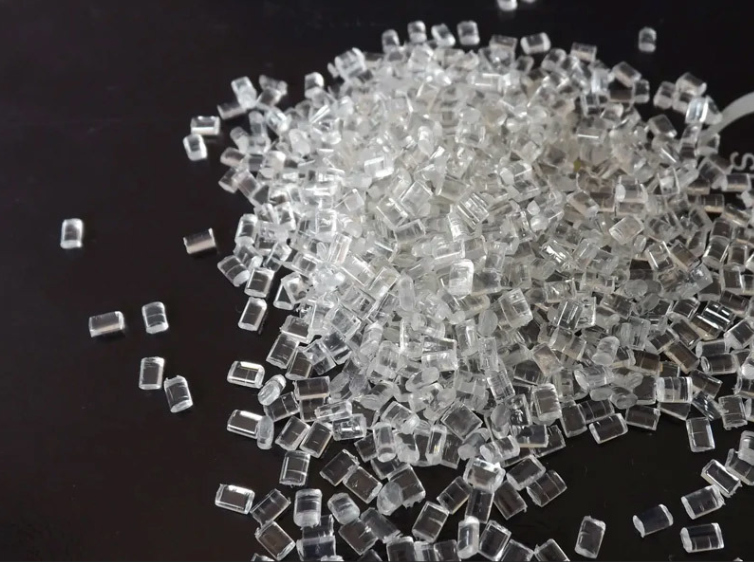
The increasingly stringent application requirements for PET recycled materials are set to drive substantial growth in industry demand, offering broad development prospects for the PET recycling sector. In this context, several types of enterprises are expected to benefit particularly: firstly, those capable of achieving high-value applications of PET recycling; secondly, companies that can expand the range of raw materials used and effectively control costs; and finally, enterprises that can overcome technological and process barriers to achieve cost-effective production of rPET using biological or chemical methods, potentially achieving breakthroughs in both cost and market share.
According to Color Masterbatch Industry Network, Sinolink Securities further elaborates on its viewpoint in the report. Physical methods, as the traditional approach to PET recycling, have a relatively solid industry foundation. However, they impose high technical requirements on enterprises during the modification and optimization of end products. Many small-scale enterprises with insufficient technical reserves often have to downgrade the application of their products. Additionally, physical recycling has high requirements for raw materials, mainly relying on PET bottles, which to some extent limits its future development potential. With the implementation of China’s policy banning the import of waste plastics, addressing the issue of raw material sourcing has become a crucial consideration for some enterprises looking to expand their business, even prompting some to plan overseas base layouts.
In contrast, chemical PET recycling is still in a phase of continuous breakthroughs, but it offers vast potential for future development. Chemical methods can significantly expand the range of raw materials for PET recycling, extending beyond bottle flakes to include fibers and films. The low recycling rate and affordable price of waste fibers help control raw material costs and further expand production scale. Although the chemical pathway is not yet fully mature, some enterprises have achieved initial technological breakthroughs. If these companies can achieve economies of scale and effectively control costs, they are likely to stand out in the industry.
Furthermore, biological PET recycling is currently still in the exploratory stage. From the perspective of reaction pathways, biological methods offer advantages in expanding the range of raw materials and achieving high-value utilization, with more room for extension in product layout directions. However, its engineering applications are not yet mature, and costs remain relatively high. Nevertheless, with the development of artificial intelligence technology, enzyme degradation processes are expected to accelerate significantly, thereby driving advancements in biological PET recycling technology.
Globally, enterprises involved in chemical PET recycling are mainly large chemical giants and startups focusing on specific areas. Large petrochemical companies, leveraging their existing industrial chain foundations, often opt for pyrolysis processes to form effective synergistic layouts and simultaneously engage in external research collaborations to explore new recycling pathways. Startups, on the other hand, often adopt new pathways or processes and lead in the research and development efforts and breakthroughs of specific technologies. However, these startups generally lack funds and engineering capabilities and experience, resulting in relatively longer implementation times for some projects.