March 12, 2025 – The film production industry has long grappled with the challenges of adhesion issues and the impact of migratory slip masterbatches on heat-sealing and printing performance. Films tend to form a vacuum-tight seal after closure, making them difficult to separate, which not only hampers production efficiency but also increases the risk of product damage. To tackle these problems, the industry commonly resorts to the addition of anti-blocking and slip masterbatches.
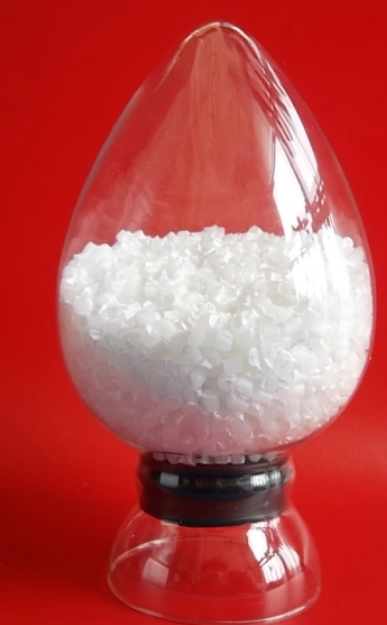
These tiny masterbatches pack a powerful punch. Their incorporation facilitates effortless unwinding and rewinding of films, while also enabling easy opening during use. Composed of carrier resin, anti-stick agents or slip agents, and various additives, the selection of anti-stick and slip agents is crucial. Options such as oleamide, erucamide, and micrometer-sized SiO2 are commonly used, each with their own set of advantages and disadvantages, necessitating careful choice based on specific application scenarios.
According to the Color Masterbatch Industry Network, film manufacturers must consider multiple factors when selecting anti-blocking and slip masterbatches. Firstly, optical performance is paramount. To achieve optimal transparency and minimal haze, the refractive index of the slip agent should closely match that of the resin, with a narrow and suitable particle size distribution. Secondly, dispersibility is key. The particle size of the anti-stick agent must be carefully chosen to ensure easy dispersion without compromising the film’s appearance and optical properties.
Furthermore, heat-sealing and printing performance cannot be overlooked. Inadequate amounts of slip agent can migrate to the film’s surface, affecting its heat-sealing and printing capabilities. Different types of films, such as aluminum-coated films, cigarette packaging films, POF heat-shrinkable films, and fruit bagging films, have their own unique requirements for anti-blocking and slip masterbatches.
For instance, aluminum-coated films require masterbatches with high wetting tension carriers and must be non-migratory. Cigarette packaging films demand masterbatches that maintain a low coefficient of friction at high temperatures without affecting the film’s gloss and transparency. POF heat-shrinkable films necessitate masterbatches with excellent and long-lasting anti-blocking and slip effects, while also preserving the film’s printing and shrinkage properties.
In summary, the selection of anti-blocking and slip masterbatches is vital in film production. Manufacturers must comprehensively consider factors such as optical performance, dispersibility, heat-sealing, and printing performance, based on specific application scenarios and demands. Only by choosing the most suitable anti-blocking and slip masterbatches can manufacturers ensure that their films exhibit exceptional performance and meet market requirements.