February 8, 2025 – Revolutionary Plastic Recycling Plant Opens in Northeast England, Capturing Global Attention
A groundbreaking factory in northeast England, launched in February 2025, has instantly drawn widespread attention from the global environmental sector. Established by London-based startup Mura Technology, this plant marks the world’s first commercial-scale application of supercritical water technology for plastic recycling. It claims the ability to magically transform mixed plastic waste, once deemed “unrecyclable,” into raw materials for recycled plastics, potentially revolutionizing the plastic recycling industry by overcoming the limitations of traditional mechanical recycling and pyrolysis techniques. Nature magazine featured this technology on its cover, heralding it as a “new antidote to the plastic pollution crisis.”
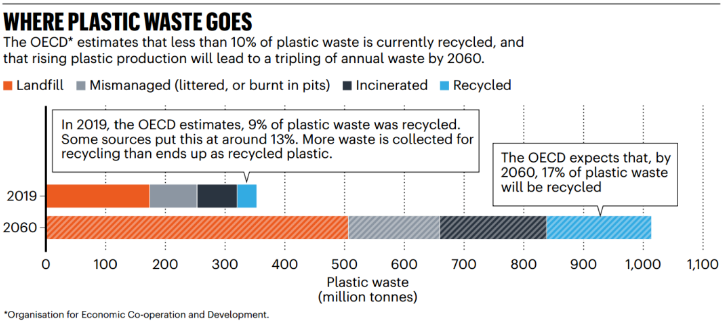
Amidst the OECD’s projection that annual global plastic waste production will surpass 1 billion tons by 2060, with a current recycling rate of less than 10%, Mura’s global expansion plan (with factories planned in Germany, the United States, Singapore, and three other countries) and the involvement of industry giants like Mitsubishi and LG Chem have injected a boost of confidence into the plastic recycling sector. The emergence of supercritical water technology not only ushers in a new chapter for the plastic circular economy but also offers a glimpse of hope for achieving a balance between environmental benefits, economic viability, and policy compliance on a commercial scale.
According to AsiaMB’s sources, Mura’s “Hydro-PRT” (Hydrothermal Pressure Recycling Technology) is the core highlight of its technological innovations. Under reaction conditions of 400°C and 220 times atmospheric pressure, water enters a supercritical state, possessing both the permeability of a gas and the solubility of a liquid, enabling uniform decomposition of plastic molecular chains. Compared to traditional pyrolysis, this technology reduces carbon emissions by 80% and can process mixed plastics contaminated with food residues, inks, and other impurities. The resulting products are hydrocarbon compounds such as naphtha and gas oil, which can be refined and resynthesized into plastic raw materials like polyethylene and polypropylene, thereby pioneering a novel plastic circular manufacturing model and significantly reducing reliance on fossil feedstocks.
However, despite its numerous advantages, including contamination tolerance, high efficiency, low carbon footprint, and flexible feedstock options, this technology faces controversies and challenges in practical application. For instance, the plant’s stringent requirements for plastic waste feedstock and the inability of some output products to be directly recycled into plastics have sparked from environmental organizations and academics. Additionally, concerns regarding the destination of products, dependence on pre-sorting, and scalability bottlenecks have raised questions about the technology’s “revolutionary” nature.
In response, governments worldwide are enacting policies and regulations to promote the sustainable development of the plastic economy. The EU mandates that plastic bottles must contain 30% recycled material by 2030, while food packaging must include 10% recycled content. The UK imposes punitive taxes on plastic packaging with less than 30% recycled content. These policies undoubtedly provide ample room for the development of chemical recycling technologies but also impose higher requirements for the authenticity and effectiveness of such technologies.