December 18, 2024 – The Challenges and Solutions in Producing Transparent TPE Pellets
The demand for transparent TPE pellets is on the rise, particularly in the production of transparent toys and components. However, many manufacturers have encountered a perplexing issue: despite using transparent TPE material, the final products often lack the desired clarity. So, what’s going on?
The answer lies in the material composition. The transparency of TPE pellets is closely linked to their compounding system, including the rubber base, processing oil, and resin additives. If the selected materials are not inherently transparent, the resulting products will inevitably suffer in clarity.
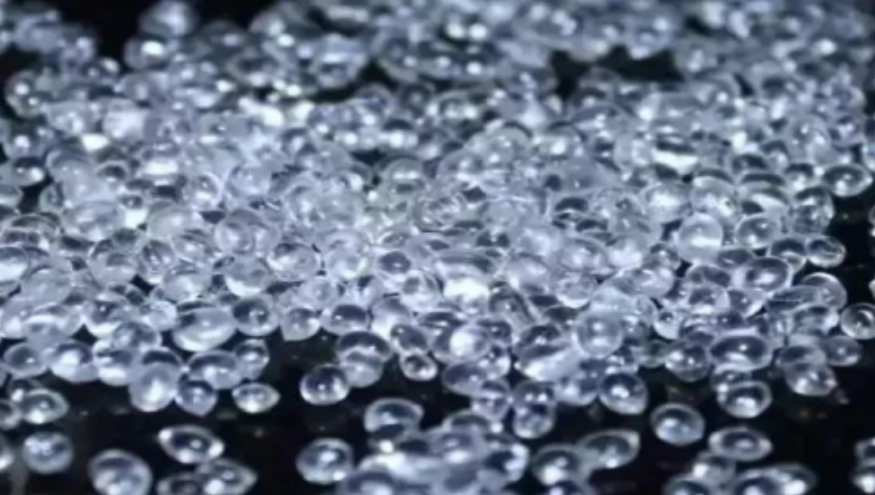
Moreover, the preparation before injection molding plays a crucial role. To ensure the transparency of TPE products, it is essential to clean the machine multiple times using a lower hardness transparent TPE material. Impurities in the screw and barrel can adversely affect the transparency of the final product, leading to unwanted black or white spots.
Plasticization is another key factor influencing transparency. As TPE is a blend of materials, different types may require different plasticization temperatures, typically ranging from 130°C to 230°C. Factors such as hardness, oil content, and the molecular weight of the rubber base can all impact the plasticization temperature. Insufficient plasticization can result in a white, opaque appearance.
High-transparency TPE materials are highly sought after in the thermoplastic elastomer market, and the requirements for the final products are stringent. They must have a uniform color and be free of defects such as pores, spots, and black dots. Therefore, close collaboration between TPE manufacturers and processors is essential to produce high-quality transparent TPE products.
Furthermore, some TPE products have strict transparency requirements, such as infusion tube catheters and glowing soft toys. To enhance the strength of TPE and TPR materials, PS or PP plastics are often added. However, this can compromise transparency. Thus, careful selection of PS and PP specifications and brands is crucial. Additionally, the amount of plastic added is a critical factor. Too much can increase hardness but reduce transparency, especially in SEBS-based TPE compared to SBS-based TPR.
In summary, achieving transparent TPE and TPR pellets requires careful consideration from the outset, starting with the selection of the compounding system components. Appropriate SEBS or SBS bases, plastic brands, and the avoidance of functional additives such as fillers, colorants, and flame retardants are essential. Moreover, the ratio of each component also affects transparency. Therefore, producing transparent TPE products is a complex process that requires meticulous attention to detail and collaboration across all stages of production.