November 29, 2024 – Since the introduction of the first commercial stereolithography 3D printer by 3D Systems in 1988, plastic 3D printing technology has undergone more than three decades of development and is demonstrating increasingly broad application prospects in the plastics industry. In recent years, this technology has garnered enthusiastic support from plastic processors, becoming a vital tool for them to enhance production efficiency, explore new markets, and even address supply chain shortcomings. Here are eight innovative applications of 3D printing technology in the plastics sector.
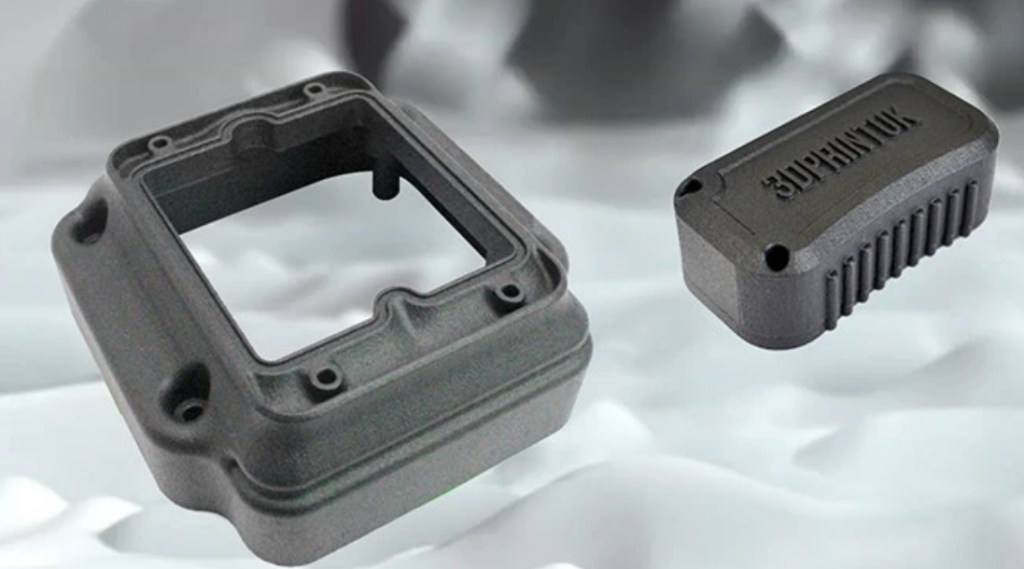
In the field of mold manufacturing, 3D printing is revolutionizing traditional processes with its unique advantages. Faced with challenges such as long mold development cycles and cumbersome design changes, 3D printing offers swift and flexible solutions. It not only accelerates the development of new molds but also easily handles repairs and modifications of existing ones. Notably, plastic 3D printing excels in rapid mold manufacturing, particularly in new product development trials, process validation, and small-batch production of multiple varieties, where it delivers significant overall economic benefits.
Furthermore, 3D printing has greatly propelled the progress of prototype design and product development. Previously, 3D printing was primarily used for rapid prototyping to validate design concepts. However, as technology advances, 3D-printed prototypes now match the performance and durability of production parts. This means designers can directly transform prototypes into final products, significantly shortening the product development cycle.
Additionally, 3D printing plays a crucial role in the production transition phase. Traditional manufacturing processes often face delays due to the unavailability of tooling. 3D printing allows manufacturers to produce parts directly while waiting for tooling, speeding up the time-to-market for new products and providing brands with valuable market feedback before committing to mold costs.
Mass customization is another highlight of 3D printing in the plastics industry. Leveraging the digital nature of 3D printing, designers can easily adjust product designs to meet specific customer or application needs. From customized medical equipment to personalized consumer products, 3D printing offers precise and efficient customization solutions.
3D printing also shows great potential in digital inventory management. Compared to traditional physical inventory, 3D printing files are easier to store and manage. This has led OEMs, military departments, and official agencies to adopt 3D printing for procuring spare parts and items required for system maintenance. By 3D printing digital inventory parts on demand, these organizations eliminate the hassle and cost of storing extra parts while achieving instant production and distribution.
Beyond these applications, 3D printing is widely used in batch production, functional product manufacturing, and fixture production. In batch production, 3D printing’s flexibility and efficiency make it a viable option for various products. In functional product manufacturing, it produces lightweight and highly integrated specialized equipment. In fixture production, 3D printing wins market recognition for its low cost and high efficiency.
In conclusion, the application of 3D printing technology in the plastics industry is continuously expanding and deepening. With ongoing technological advancements and the emergence of innovative applications, we have reason to believe that 3D printing will bring even broader development prospects and limitless possibilities to the plastics sector.