November 13, 2024 – ISBM Technology: Revolutionizing Plastic Packaging with Efficiency and Flexibility
In the plastic packaging industry, ISBM (Injection Stretch Blow Molding) technology has emerged as a favorite due to its efficiency and flexibility. This advanced technique is widely applied to various materials such as PET, PETG, PCTG, Tritan, PC, SAN, PP, and PA, producing a myriad of containers including carbonated beverage bottles, energy drink bottles, water bottles, beer bottles, and various food and non-food contact containers. This article delves into the material applications, process evolution, and critical design and processing elements of ISBM technology.
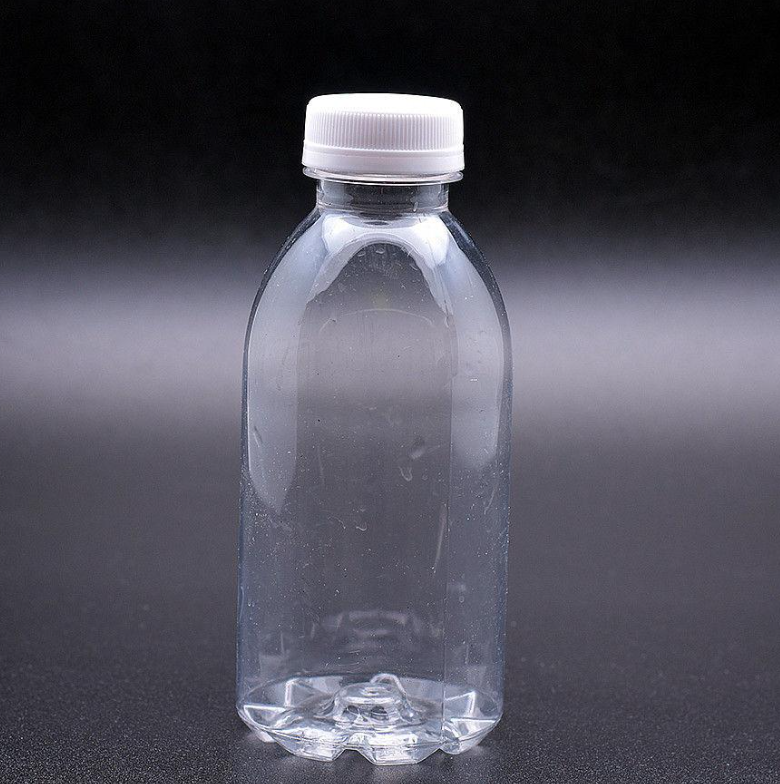
ISBM technology, a type of blow molding process, has evolved through stages including extrusion blow molding (EBM), injection blow molding (IBM), and reheat stretch blow molding (RHB). Among them, ISBM integrates both injection molding and blow molding processes into a single machine, enabling one-step molding from plastic pellets to the final bottle shape, significantly boosting production efficiency. According to AsiaMB, this technology is particularly suited for copolyester materials like Tritan, capable of producing high-quality bottles at lower costs.
In the practical application of ISBM technology, the design of the preform is a crucial aspect. Design parameters such as the blow-up ratio, axial stretch ratio, and hoop stretch ratio of the preform directly influence the quality and performance of the final product. For instance, Tritan material is suitable for designs with a small stretch ratio, whereas traditional PC water bottles employ a large stretch ratio. Additionally, the wall thickness, draft angle, and gate design of the preform are also key factors affecting product quality. Designers must comprehensively consider material properties, product usage, and production process requirements to formulate an optimal preform design plan.
However, during the ISBM molding process, manufacturers often encounter processing issues such as preform sticking to the mold, gate eccentricity, orange peel effect, and flow marks. These problems are typically attributed to factors including material selection, equipment configuration, injection and blow molding process parameters, and preform design. To address these challenges, manufacturers need to implement a series of improvement measures, including optimizing preform and bottle design, selecting appropriate materials and equipment, adjusting process parameters, and strengthening quality control throughout the production process.
Moreover, the drop impact resistance of ISBM bottles is a critical consideration in product design. To enhance the drop resistance of bottles, designers must focus on details such as optimizing product design, draft angle, and bottom structure to improve the impact strength of the product. Mold design is also crucial, as the choice of clamp edge material, cooling system configuration, and mold temperature setting directly affect the molding quality and performance of the product.
In summary, ISBM technology stands as a significant molding method in the plastic packaging industry. Its material applications, process development, and key design and processing elements warrant in-depth research and discussion. Through continuous optimization and innovation, we can produce higher-quality, lower-cost plastic packaging products to meet the diverse needs of the market.