October 30, 2024 – revolutionizing Industries with Anti-Fog Technology: An In-Depth Look into Anti-Fog Additives and Their Mechanisms
The seemingly innocuous issue of fogging on plastic lids of food or car windshields during humid weather can actually pose significant troubles for various industries. This is where anti-fog technology comes into play, playing a crucial role by preventing the formation or adhesion of water droplets, thus ensuring clarity and optimal performance of products. In this article, we delve into the types of anti-fog additives and their working mechanisms.
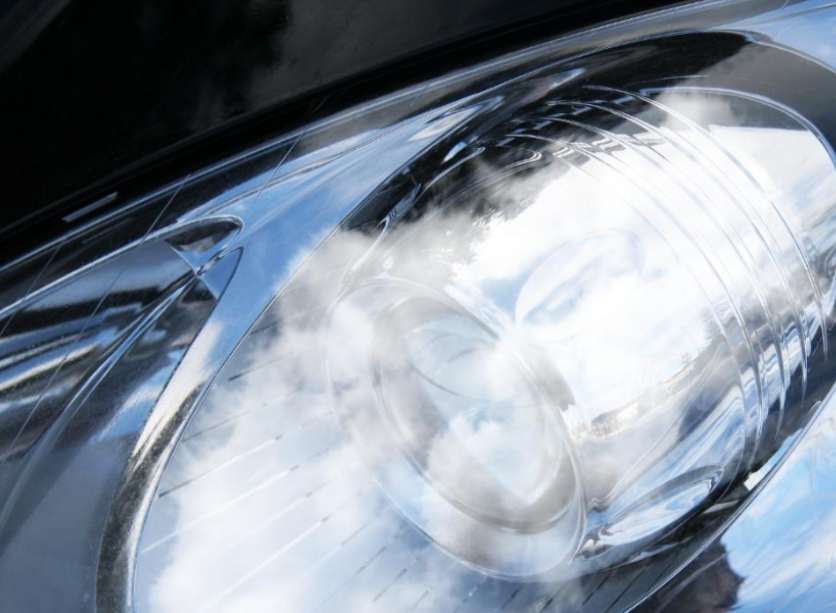
The world of anti-fog additives boasts a diverse range, tailored for different operating environments. To effectively combat fog, it’s essential to understand the chemical fundamentals. Surfactants, due to their amphiphilic nature, are a powerful tool in the anti-fog domain. They can dissolve in the aqueous phase and control the dissolution process through hydrophilic-hydrophobic balance. These small additive molecules quickly migrate to the polymer surface, exerting their anti-fog effect.
In addition to surfactants, polymers also form an integral part of anti-fog additives. Both synthetic and natural polymers can be used to create anti-fog surfaces, with natural polymers being particularly favored due to their non-toxic and environmentally friendly properties. Furthermore, inorganic compounds such as SiO2, In2O3-SnO2, also play pivotal roles in anti-fog applications. They can exist in forms like solid or hollow nanoparticles or be chemically and physically modified to become super hydrophilic materials, effectively preventing fogging.
According to the Color Masterbatch Industry Network, various methods exist to achieve anti-fog surfaces, primarily including internal addition, external coating, and surface modification. Internal addition involves incorporating anti-fog additives in the form of masterbatches into plastics, with these additives continuously migrating to the plastic surface over time to form a hydrophilic layer. External coating, on the other hand, involves applying an anti-fog coating to the plastic surface. This coating is translucent, abrasion-resistant, and durable, effectively preventing water from condensing on the surface. Surface modification alters the chemical properties of the polymer surface through methods such as plasma, corona, or flame treatment, improving its wettability.
In terms of choosing anti-fog coatings, they can be classified into organic, inorganic, and inorganic-organic based on their chemical properties. Organic coatings achieve anti-fog effects by depositing natural or synthetic water-soluble polymer films with hydrophilic properties. Inorganic coatings are more durable, scratch-resistant, wear-resistant, and resistant to chemical degradation. Inorganic-organic coatings combine the advantages of both, exhibiting superior anti-fog performance.
In summary, anti-fog technology, through different types of additives and various implementation methods, offers effective solutions for various industries. Whether it’s food packaging, car windshields, or other fields, suitable anti-fog solutions can be found to meet specific needs.