October 19, 2024 – The global polyethylene market is set for significant growth, according to predictions from renowned UK-based data firm Global Data. By 2020, the worldwide production capacity of Low-Density Polyethylene (LDPE) is anticipated to surge from 26 million tons per annum in 2015 to 34 million tons per annum. China, in particular, is experiencing substantial growth in both production capacity and consumption of polyethylene, fueled by a sharp rise in demand from the film market, which has driven the annual increase in LDPE output.
Currently, nearly 90% of polyethylene plants in China that utilize gas-phase and high-pressure processes are dedicated to producing low-density, low-melt index film materials. These materials primarily fall within the density range of 0.915 to 0.925 g/cm³ and have a melt index of 0.8 to 2.5 g/10min. Among these, the DFDA-7042 and DFDA-7047 series have the highest production volumes.
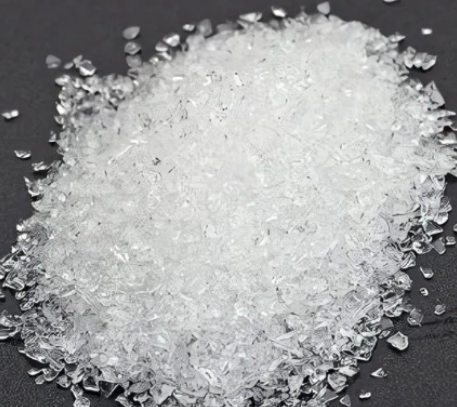
As AsiaMB learns from the Color Masterbatch Industry Network, the proliferation of rapid packaging lines in China has necessitated upgrades in packaging materials, leading to increased demands for polyethylene films with improved ease of opening and reduced haze. Given the wide variety and high addition levels of opening agents and slip agents domestically, research into these additives is crucial and holds significant importance for advancing China’s polyethylene film materials.
Challenges and Solutions in Polyethylene Film Opening
The poor opening performance of polyethylene films can be attributed to four main factors: the presence of exposed molecular chain ends and low-polymer small molecules on the film surface after processing, which easily intertwine; significant van der Waals forces between adhered films; vacuum sealing during the film blowing process; and increased static accumulation due to higher film production speeds, resulting in static adhesion. To address these issues, methods such as incorporating inorganic opening agents to increase film spacing and reduce vacuum levels, adding slip agents to form a slip layer and reduce molecular chain entanglement, and introducing antistatic agents to eliminate static adhesion are commonly employed.

Selection and Application of Opening and Slip Additives
1. Opening Agents
Inorganic opening agents, such as talc, kaolin, and silica, are typically chosen. These agents create an uneven surface on the film, increasing the spacing between films and reducing negative pressure, thereby facilitating easier opening. Silica, in particular, is a preferred choice due to its porous structure, high specific surface area, and similar refractive index to polyethylene. However, considerations such as particle size selection, adjustment of thermal stabilizer and halogen absorber addition levels, type selection, and enhanced dispersibility are essential when using these agents.
2. Slip Agents
Also known as organic opening agents, slip agents primarily consist of long-chain fatty acid amide compounds. When added, they form a slip layer on the film surface, reducing the coefficient of friction between films. The choice of slip agent depends on the length of the fatty acid chain to achieve optimal migration speed and aging effect.
3. Antistatic Agents
In high-speed printing or automatic packaging films, static electricity can easily occur, affecting production and film performance. The addition of antistatic agents can effectively reduce the static potential. Commonly used antistatic agents include glycerol monostearate and fatty acid amines.
Production Recommendations for High-Opening, High-Slip LDPE Grades
During the production of high-opening, high-slip films, the high addition levels of inorganic opening agents and slip agents can lead to increased film haze and even additive precipitation. To address these issues, it is recommended to add polymer processing aids (PPA) such as fluoroelastomers, which can reduce friction between the melt and metal, lower energy consumption, and improve film optical properties. Additionally, considering the addition of organic nucleating agents to increase the crystallization temperature of polyethylene, induce heterogeneous crystallization, and reduce haze is advisable. However, attention should be given to the cost and dispersibility of these additives.
Conclusion
To meet the market’s escalating demand for high-transparency, low-haze polyethylene films, manufacturers should comprehensively consider the selection, ratio, and synergistic effects of various additives. Polyethylene producers are advised to refine their product grades based on the end-use applications of films, enhancing product quality and corporate profits while avoiding the increased costs associated with excessive additive usage.