October 17, 2024 – The role of fillers in enhancing material properties is a multifaceted and intricate subject, characterized by their extensive utility and diverse functionalities. As a bulking agent, fillers effectively contribute to reducing product costs while also modulating the viscosity and flow characteristics of molding systems, thereby optimizing processing conditions. In terms of improving the physical and mechanical properties of products, fillers excel, enhancing mechanical strength, heat resistance, and reducing thermal expansion and molding shrinkage rates, alongside bolstering abrasion resistance. Furthermore, they impart novel attributes such as conductivity, magnetism, piezoelectricity, sound insulation, and shock absorption, significantly broadening the application spectrum of plastic materials.
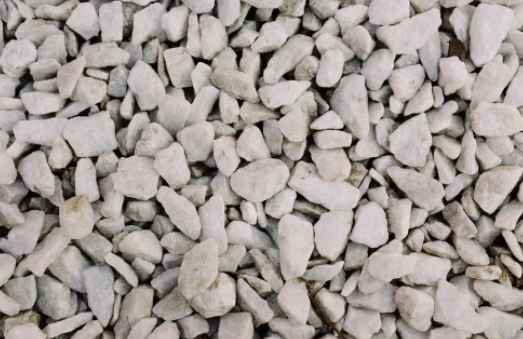
Regarding hardness, the incorporation of fillers notably elevates the modulus and hardness of filled plastics. Hardness assessments, commonly conducted through ball indentation and Shore hardness methods, with the former offering a more accurate representation of the actual hardness of filled plastics, underscore this enhancement. According to insights from ColorMasterbatchIndustry.com, filler particle size and loading have a pronounced impact on friction performance; finer particles and higher loadings tend to decrease the friction coefficient, whereas harder fillers may increase wear on processing equipment but enhance the wear resistance of the filled plastic.
In thermal performance, fillers substantially raise the heat deflection temperature of filled plastics and lower the coefficient of thermal expansion, enhancing product dimensional accuracy. Additionally, the specific heat capacity and thermal conductivity of fillers influence the compounding, thermoforming, and cooling processes of filled plastics. By judiciously selecting and controlling filler types and loadings, optimal thermal performance can be achieved to cater to various application requirements.
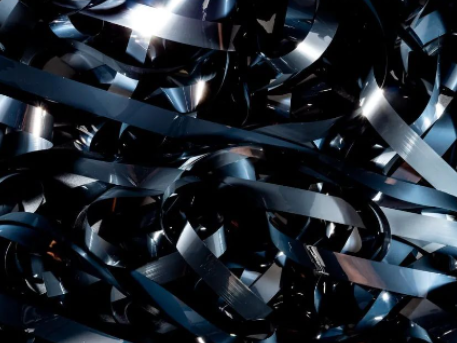
Optical functional fillers, such as glass beads, find widespread use in traffic signs and automotive coatings, leveraging light reflection and scattering effects for specific functionalities. Moreover, far-infrared radiation functional fillers demonstrate significant potential in promoting plant growth, ripening fruits, facilitating fermentation, and providing thermal insulation for humans.
In the realm of electrical properties, the addition of fillers serves as an effective means of enhancing plastic antistatic properties. Conductive fillers like metal powders, graphite, and carbon black notably improve plastic conductivity, enabling the production of permanently antistatic plastics. These conductive fillers hold substantial value in applications such as underground mining and computer components.
Magnetic plastics, a special class of functional plastics, exhibit immense potential in the electronics industry. By incorporating magnetic fillers such as ferrite or rare-earth magnetic powders, plastics with exceptional magnetic properties can be produced. These magnetic plastics, characterized by lightweight, flexibility, and minimal post-molding dimensional shrinkage, are widely applicable in various electronic and electrical components.
In conclusion, the application of fillers in plastic materials is marked by its breadth and diversity. Through careful selection and combination of filler types and loadings, the performance and application scope of plastic materials can be significantly optimized.