October 14, 2024 – Major Breakthrough for Hangyang’s Chemical Project: First 110,000-Grade Air Separation Unit Achieves Oxygen Output
Hangyang, a leading state-owned enterprise in the field of air separation, has recently made significant progress in a major chemical project. On October 9th, the first 110,000-grade air separation unit successfully achieved oxygen output, marking a solid step forward for the world’s largest single-plant olefin factory and green hydrogen-substituted fossil fuel olefin production project.
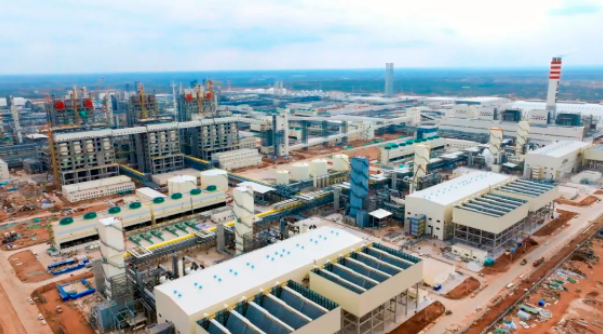
This milestone project not only boasts an impressive scale but also showcases remarkable technological innovation. It innovatively integrates green hydrogen with modern coal chemical production processes, with a total capacity of 3 million tons per year. Notably, 400,000 tons of products are produced through the substitution of coal with green hydrogen, a crucial move in reducing fossil fuel consumption and lowering carbon dioxide emissions. Hangyang’s internationally leading design and manufacturing capabilities, coupled with its professional and efficient technical services, have provided a strong guarantee for the successful implementation of this project. This achievement also serves as a tribute to the 75th anniversary of the founding of New China.
According to the Color Masterbatch Industry Network, Hangyang has maintained a robust development momentum in the market for ultra-large air separation equipment. In recent years, it has secured multiple orders for ultra-large air separation units, including those from Shenhua Ningxia, Shenhua Yulin, Zhejiang Petrochemical, and Baofeng Energy. Currently, Hangyang leads the global air separation market, with its products widely used in key industries such as chemicals, metallurgy, fertilizers, semiconductors, optical fibers, aerospace, research, and healthcare. In particular, Hangyang has sold 139 sets of air separation equipment above the 60,000-grade level, with 29 sets above the 100,000-grade level, demonstrating its strong prowess in the field.
Furthermore, Hangyang is actively promoting the deep integration of air separation equipment with digitization. Through its smart operation center, it achieves real-time monitoring and process tracing, ensuring stable, energy-saving, and environmentally friendly equipment operation. This initiative not only enhances the performance and efficiency of air separation equipment but also leads the domestic air separation industry towards high-end, refined, and intelligent development.
With a total investment of 67.3 billion yuan, this project aims to substitute coal for petroleum and new energy for fossil fuels, establishing the world’s largest single-plant olefin factory. The project is planned to produce 13.25 million tons of methanol, 5 million tons of olefins, 2.5 million tons of polyethylene, and 2.5 million tons of polypropylene annually. The methanol production alone accounts for over 16% of the national total, while olefin production accounts for over 9%. The first phase of the project, with an investment of 47.8 billion yuan, has an annual production capacity of 7.42 million tons of methanol, 3 million tons of polyolefins, 1.5 million tons of polyethylene, and 1.5 million tons of polypropylene. Notably, the project also utilizes “wind-solar integration” technology to generate 2.5 billion cubic meters of green hydrogen, substituting coal and petroleum to produce 1.17 million tons of green methanol and 400,000 tons of green olefins. This makes it one of the world’s largest chemical production enterprises using new energy to substitute fossil fuels.
Upon completion, the project is expected to generate an annual revenue of over 60 billion yuan, add 40 billion yuan to industrial value, and contribute over 6 billion yuan in taxes, while providing employment for over 10,000 people. This will inject new momentum into local economic prosperity, industrial transformation and upgrading, and national energy security. Additionally, it will open a new chapter in the scientific development path towards “carbon neutrality” in the energy and chemical industry.